案例研究
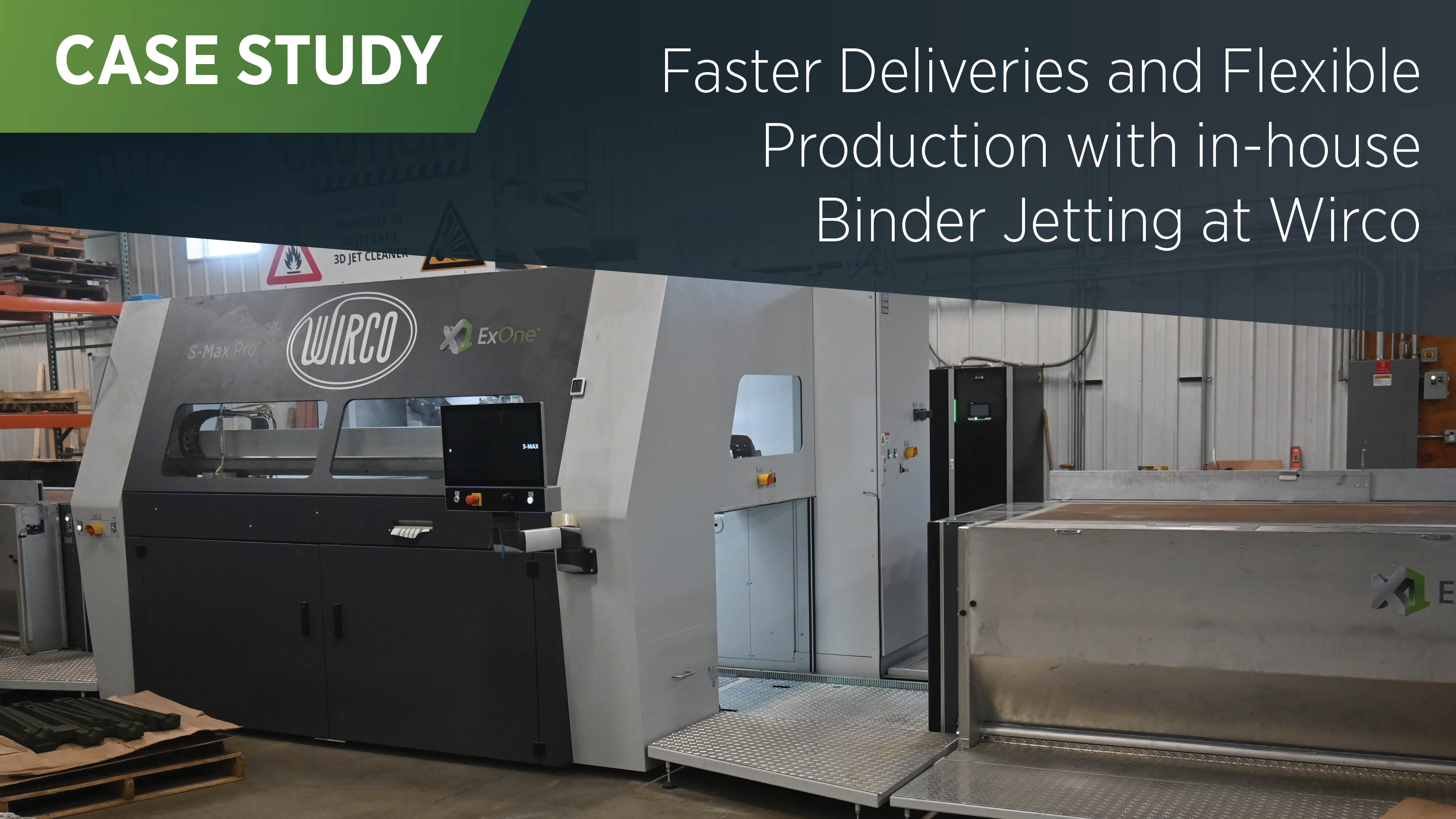
Faster Deliveries and Flexible Production with Binder Jetting
How Wirco’s investment in sand 3D printing technology paid off in speed, precision, and flexible manufacturing solutions
Case Study: Wirco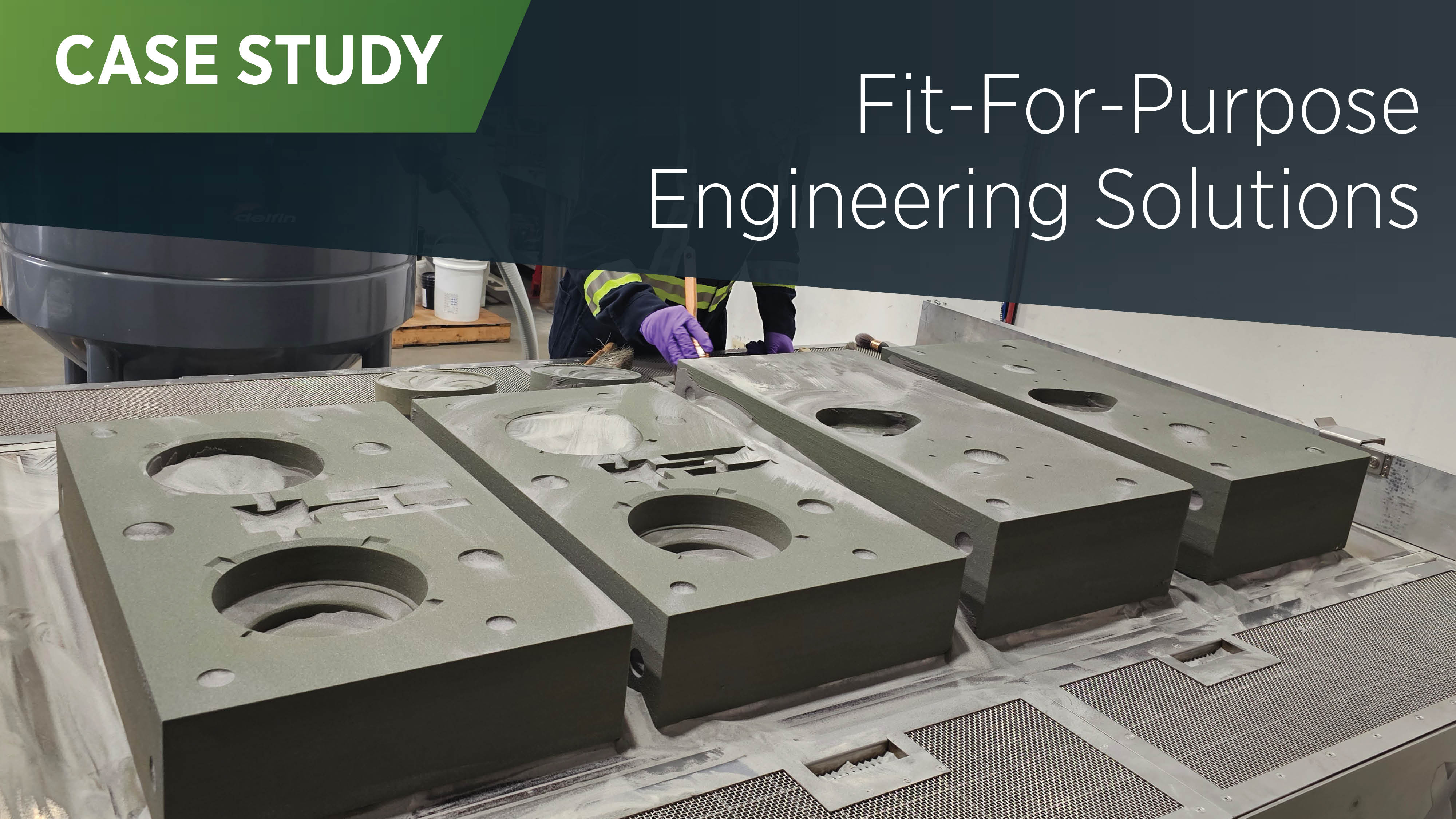
3D Printed Tooling Enables Quick-Turn Castings to Reduce Downtime
Demir Engineering invested in binder jetting for quick-turn metalcasting rapid replacement parts that limit expensive downtimes
Case Study: Demir Engineering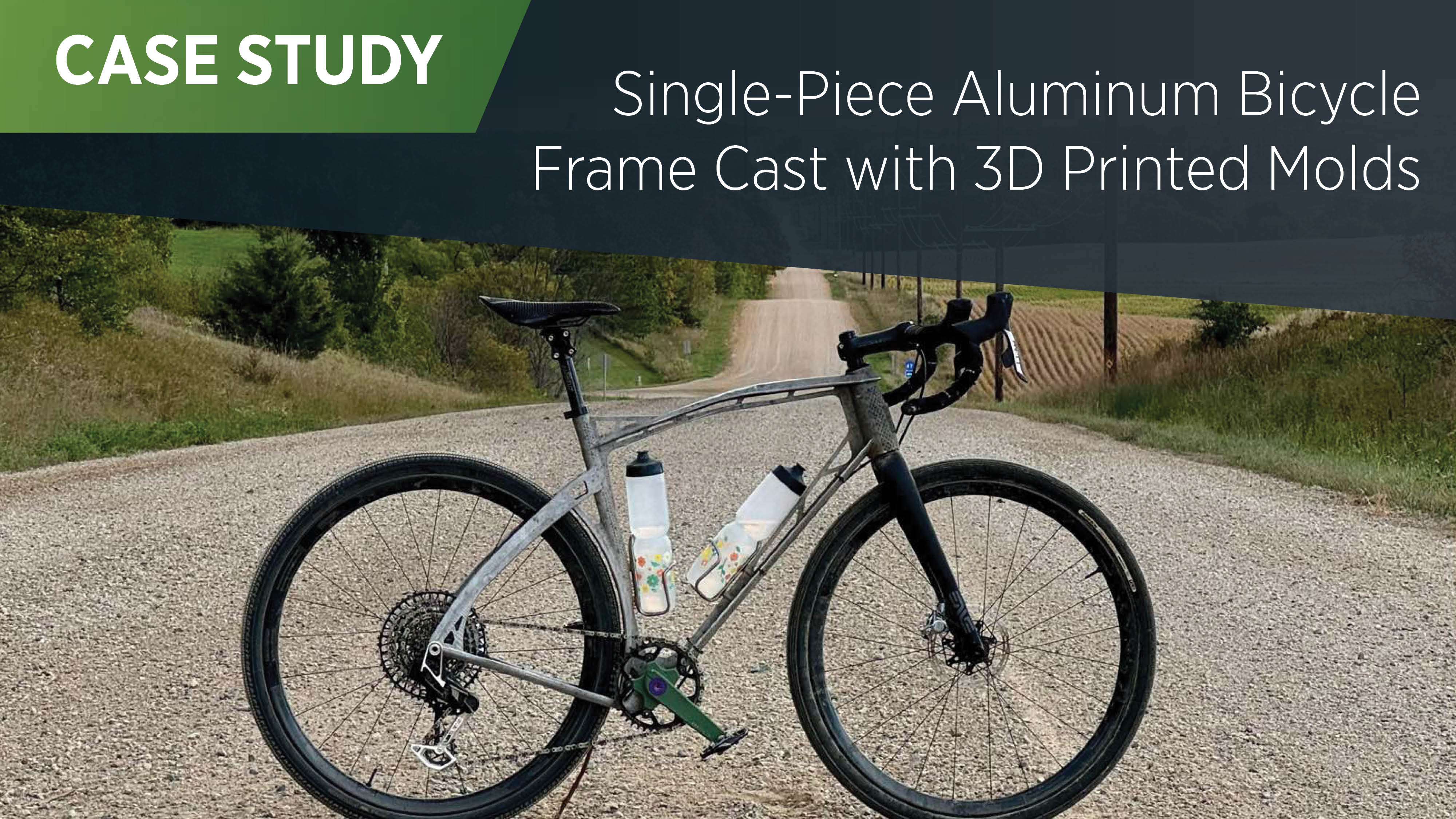
Single-Piece Bike Frames Cast in Aluminum with 3D Printed Molds
Binder jetting helps produce a more confidence-inspiring ride without welds while enabling customizations to expand access
Case Study: Heavy Bikes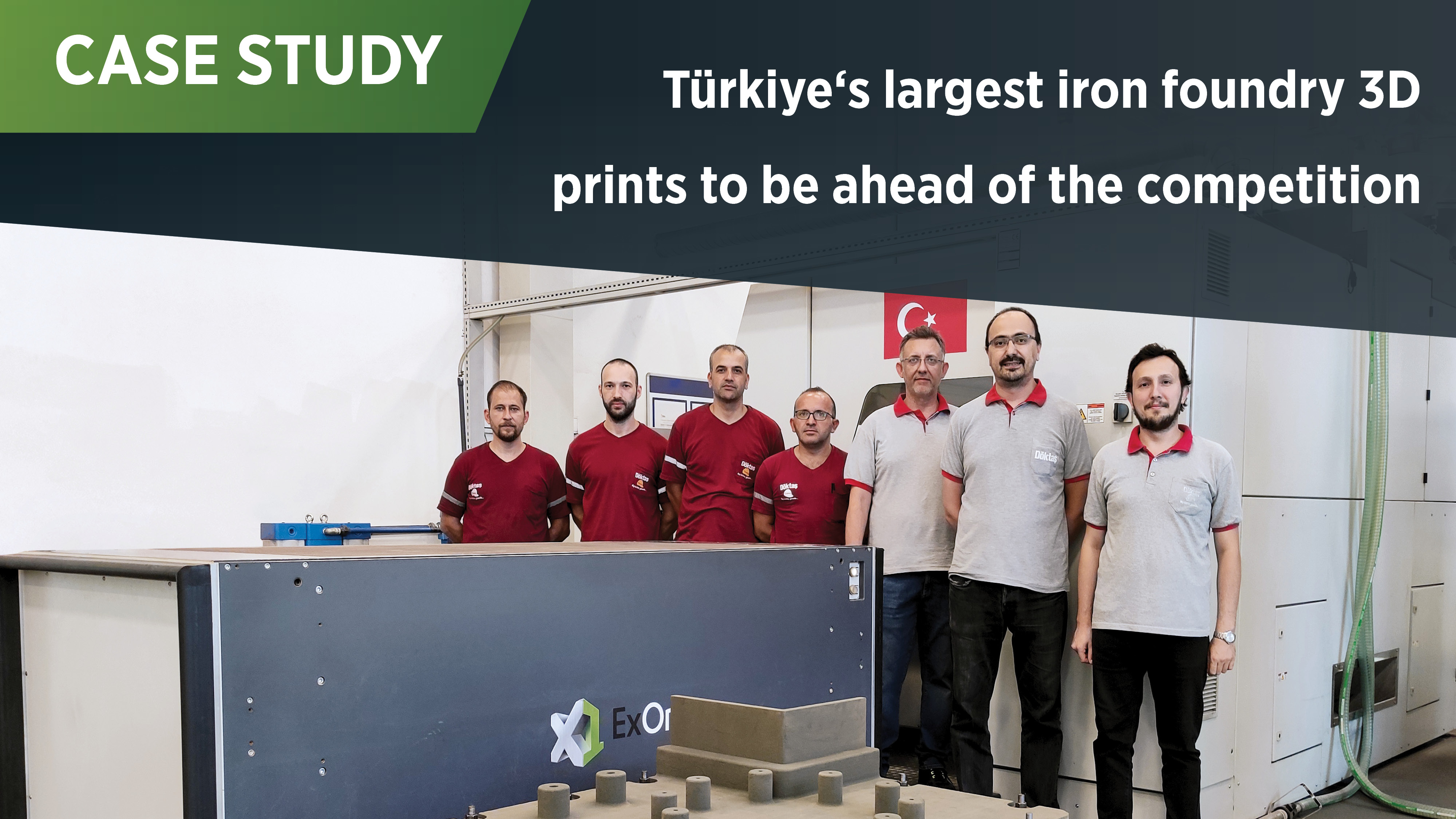
Shorter time to market and agility in production with sand binder jetting.
Döktas, the first foundry in the world to use ExOne S-Max Pro, leverages 3D printing for rapid prototyping and serial production
Case Study: Döktas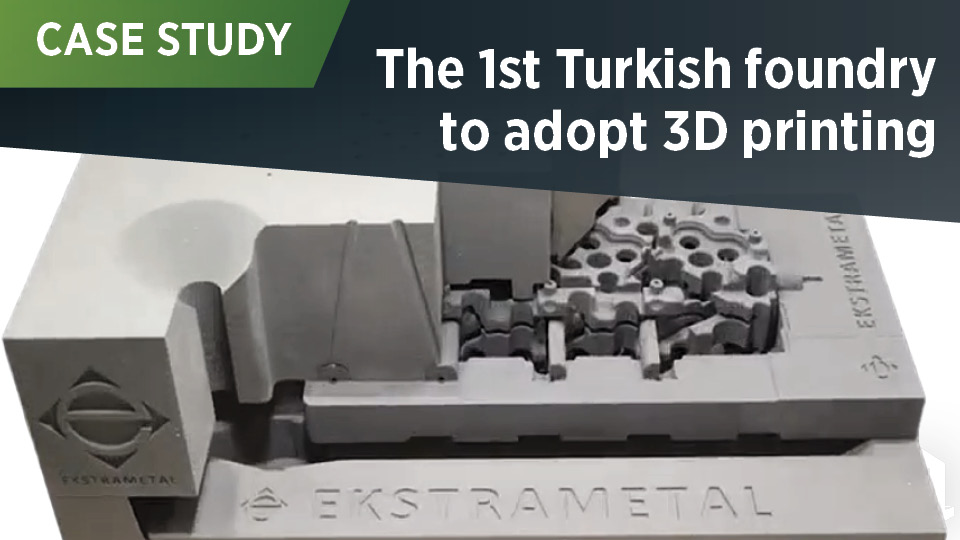
Efficiency and Precision through Sand 3D Printing in Iron Casting
Ekstrametal delivers top-quality cast parts by 3D printing molds and cores for rapid prototyping, short series productions, and GJV-450 machining fixture.
Case Study: Ekstrametal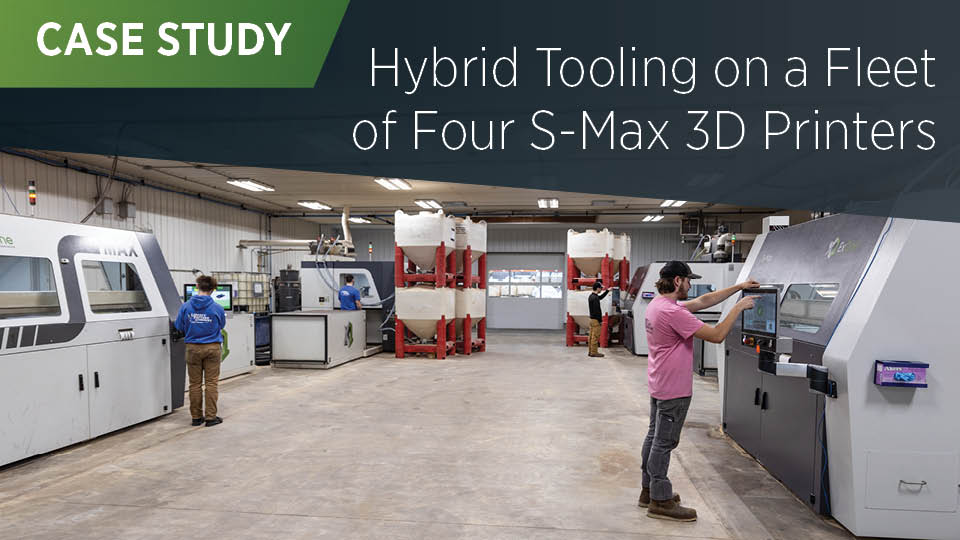
Traditional Pattern Shop Users Binder Jetting for Hybrid Tooling
Liberty Pattern adopt binder jet 3D printing at its facility in Iowa for complex core production and quickly grows to fleet of four machines
Case Study: Liberty Pattern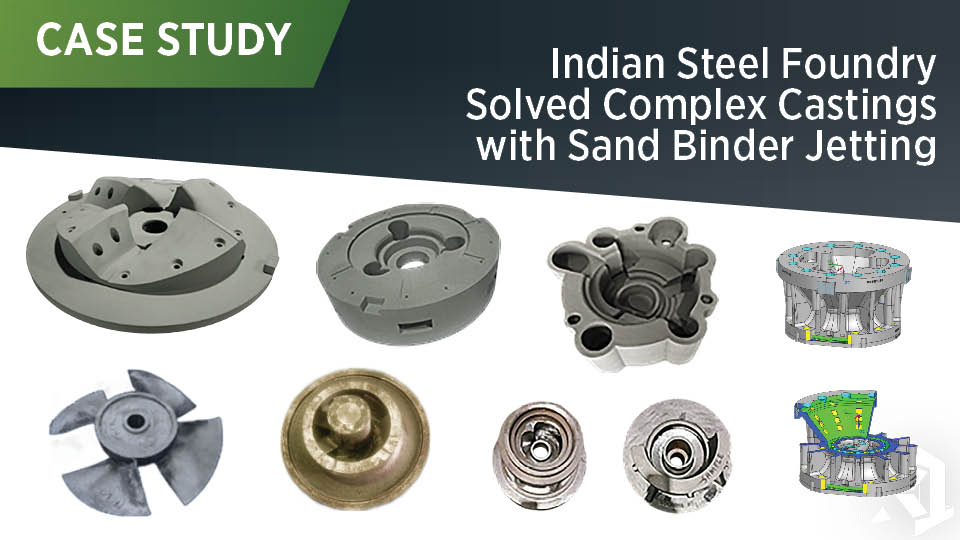
Indian Steel Foundry Solved Complex Castings with Sand Binder Jetting
Digital casting with ExOne S-Max® 3D printer enables KSB in India to drastically reduce lead times, improve part quality, and lower production costs
Case Study: KSB India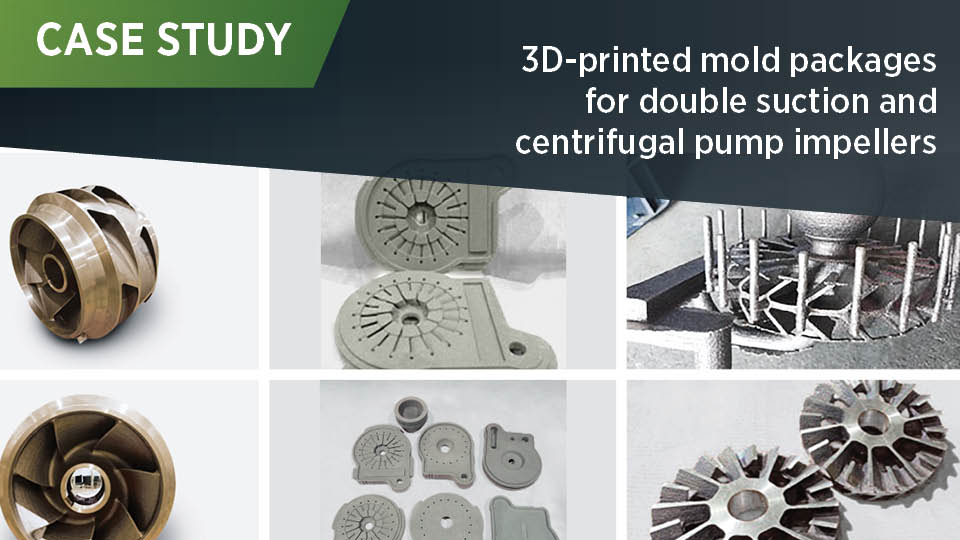
Rapid and cost-effective casting of complex impellers
Speed 3D Mold accelerates delivery time of a complex casting & achieves efficient, low-volume production with sand 3D printing
Case Study: Speed 3D Mold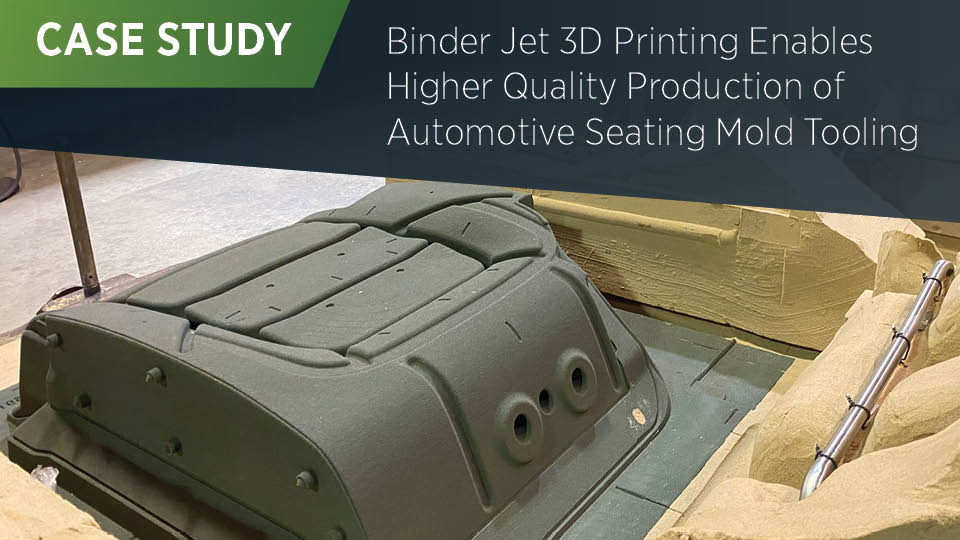
Binder Jetting for Higher Quality Automotive Seating Mold Tooling
Millions of automotive seats benefit from 3D printing technology at Dundee Castings’ to deliver updated tooling designs
Case Study: Dundee Castings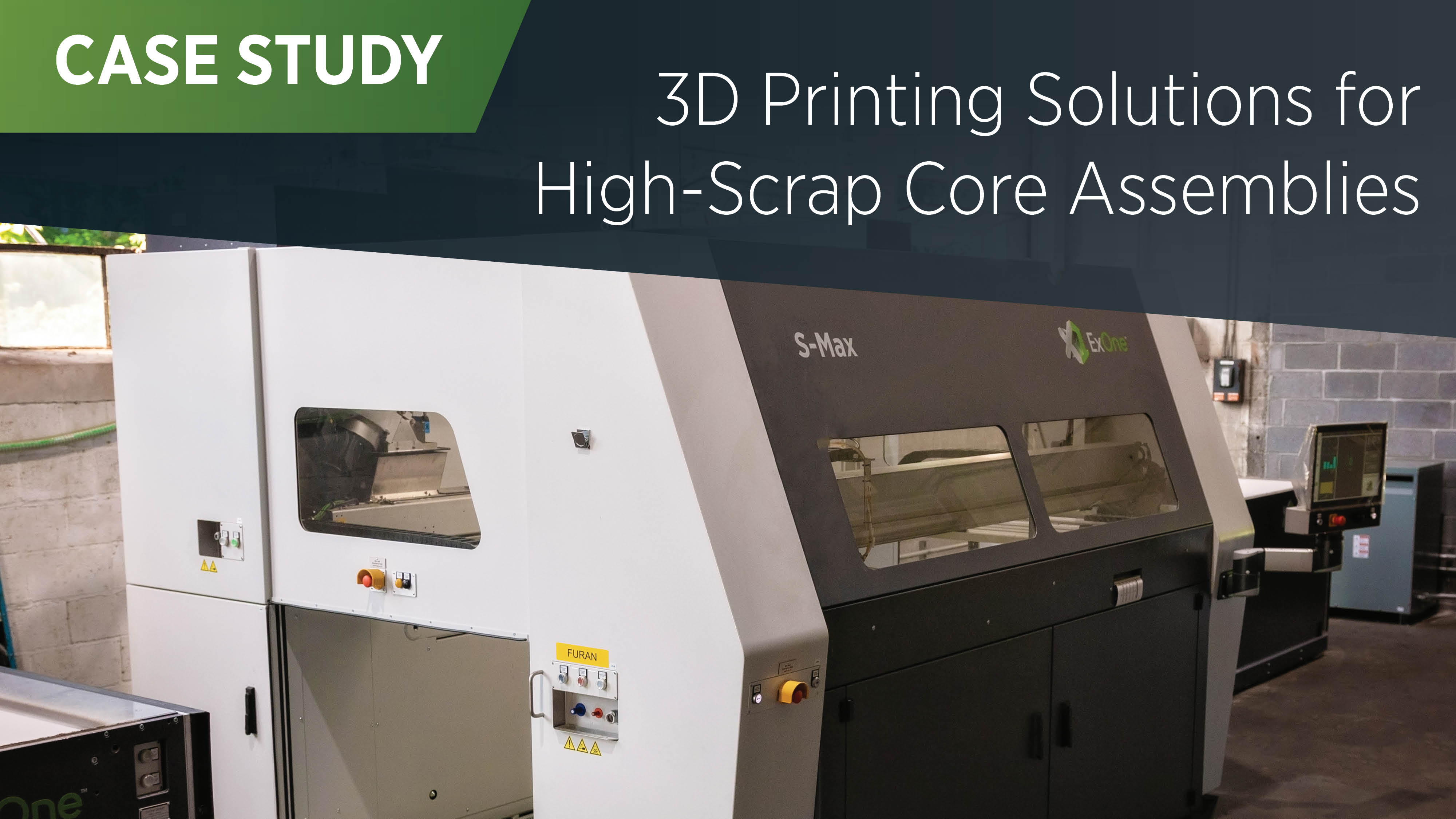
3D Printing Solutions for High-Scrap Assembled Cores
Kore Mart adopts S-Max® binder jet sand 3D printing system for top-quality cores that eliminate complex assemblies - even at serial production levels
Case Study: Kore Mart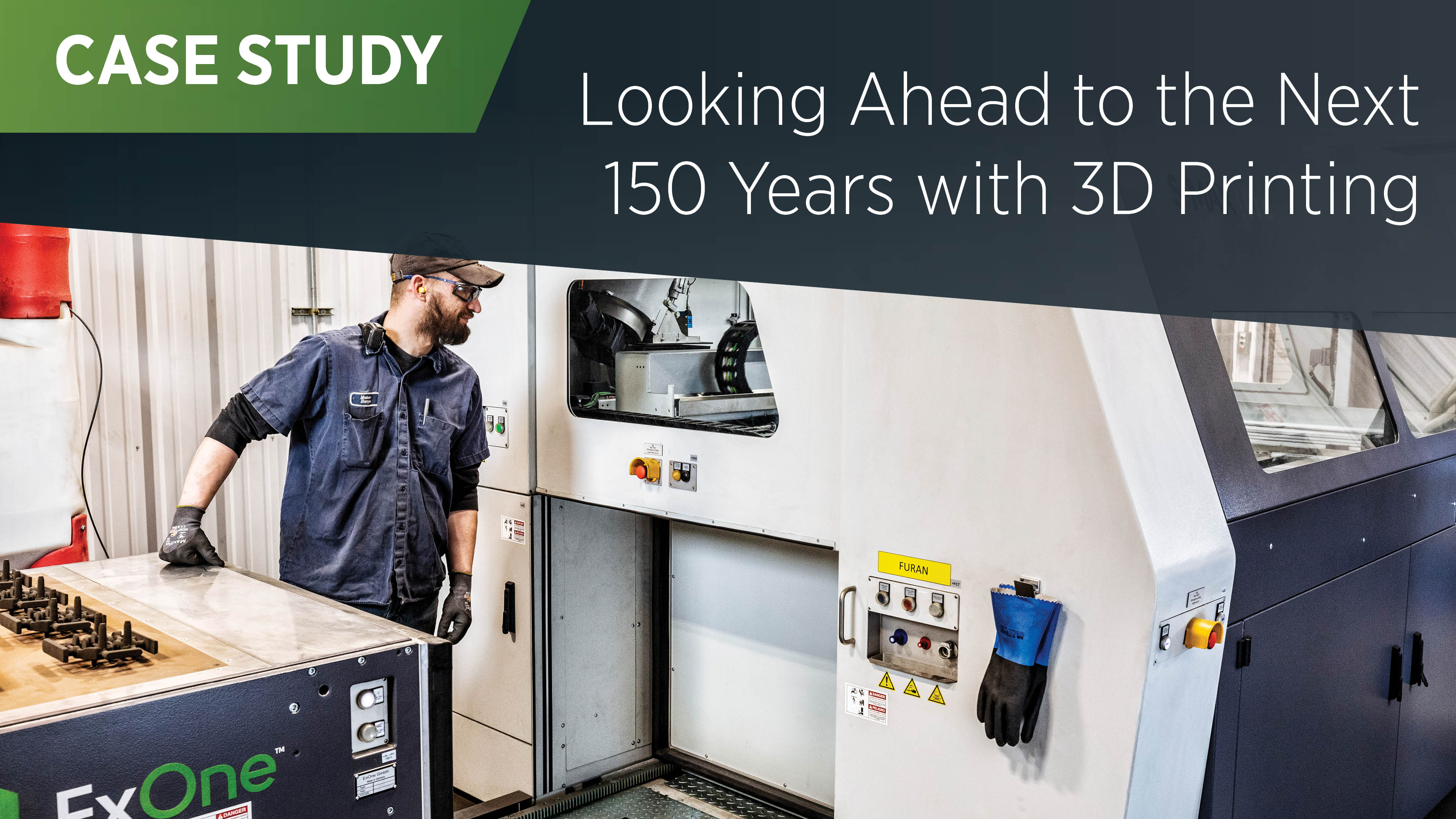
Looking Ahead to the Next 150 Years with Binder Jet 3D Printing
Waupaca Foundry fuses tradition and technology by bringing binder jet sand 3D printing in-house
Case Study: Waupaca Foundry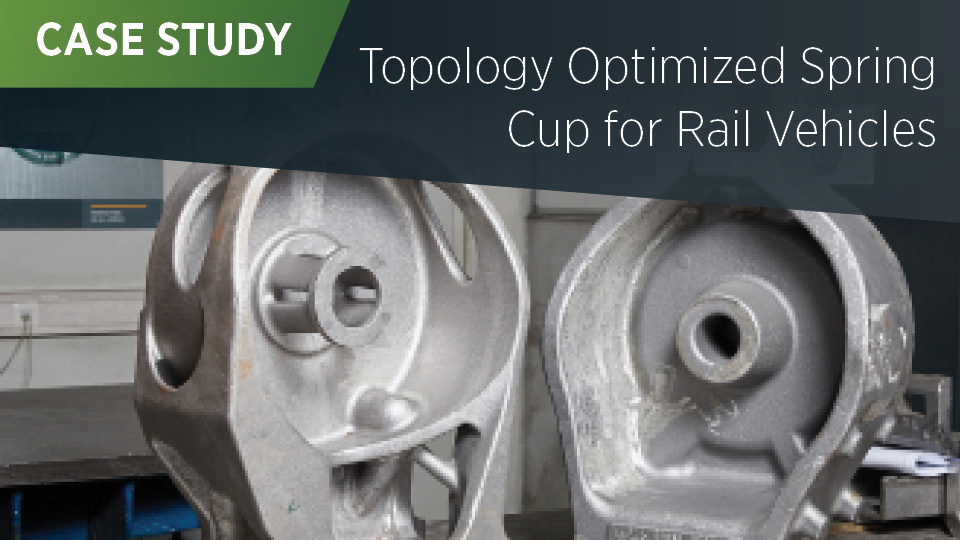
Topology Optimized Spring Cup for Rail Vehicles
An award-winning research project of topology optimization enhancement with 3D sand printing for a lighter and longer lasting spring cup for rail vehicles
Case Study: MFL and ÖGI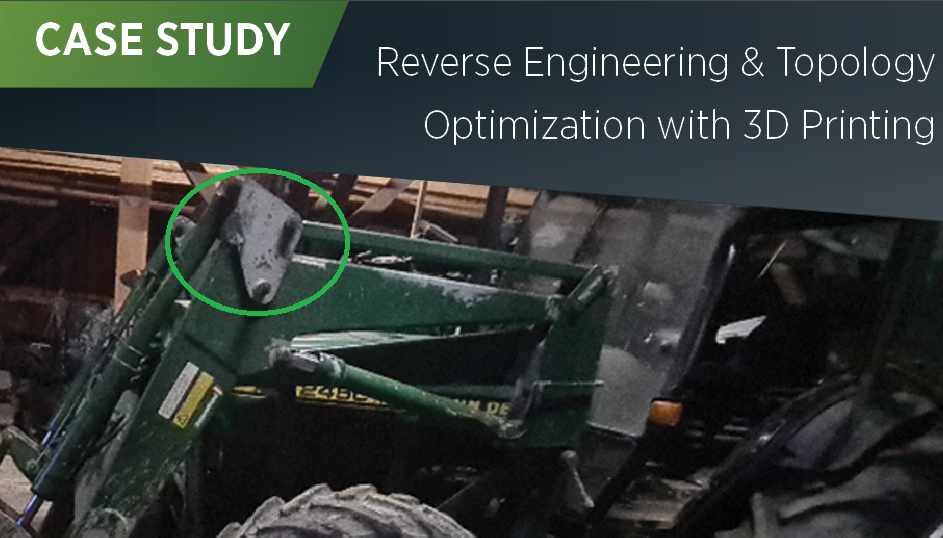
Reverse Engineering and Topology Optimization with 3D Sand Printing
Replacement of a welded steel agricultural machine construction with a topology optimized casting within one week
Case Study: ÖGI (Austrian Foundry Institute)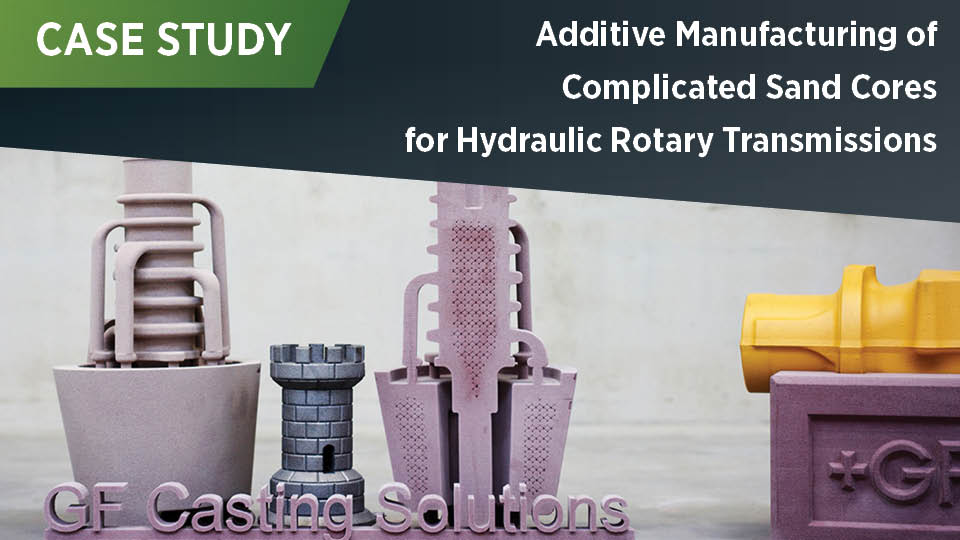
Georg Fischer Casting Solutions Leipzig consolidates 12 shot cores into one printed core
In addition to improving the core quality, time-intensive and laborious core assembling and fettling steps are eliminated.
Case Study: GF Casting Solutions Leipzig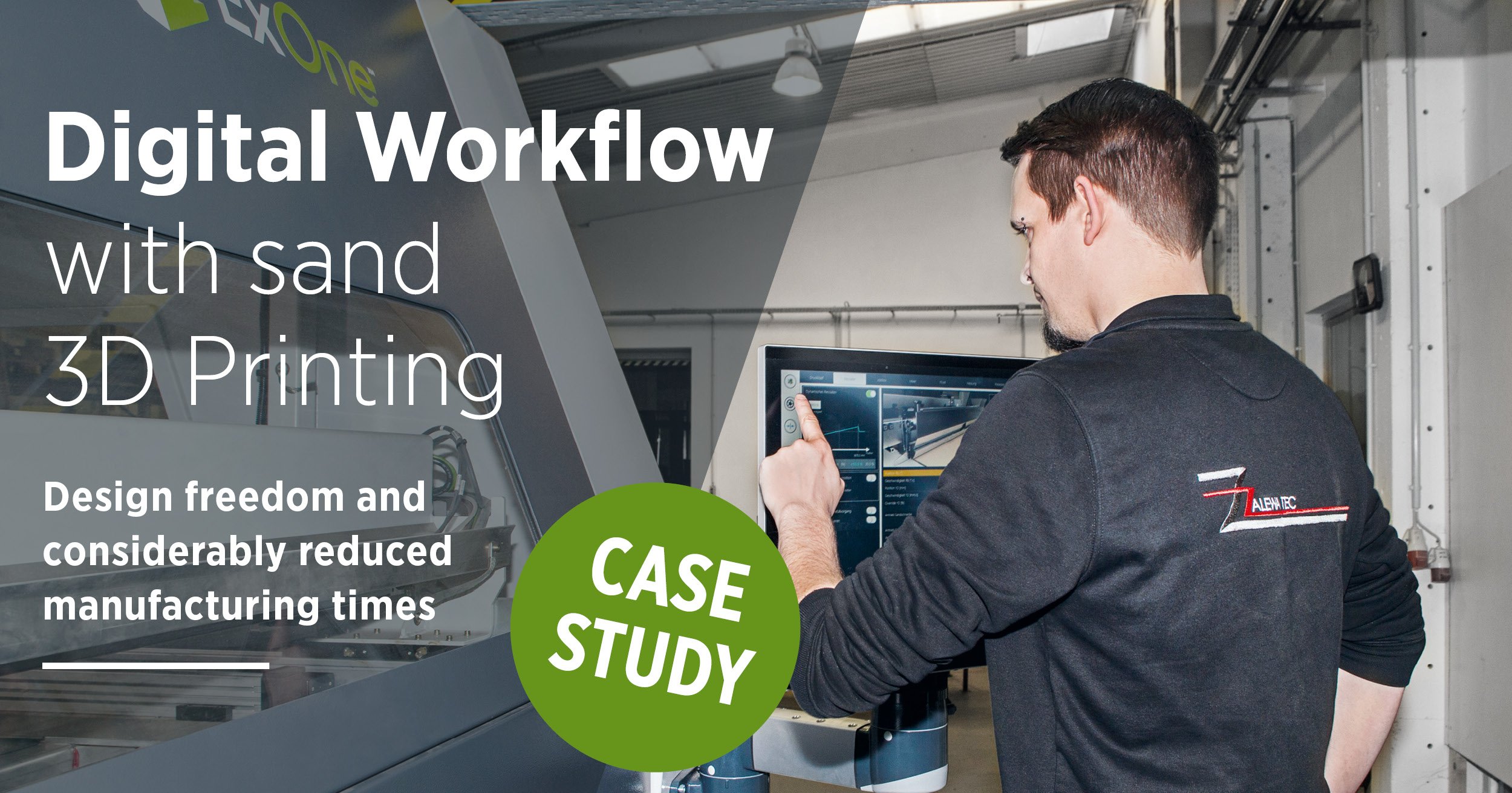
Successful European Start-Up Supports 3D Printing for Foundries and Beyond
A completely digital workflow built around the ExOne S-Max® enabled start-up Zalewa Tec to quickly establish itself as a premium manufacturer of sand molds and cores
Case Study: Zalewa Tec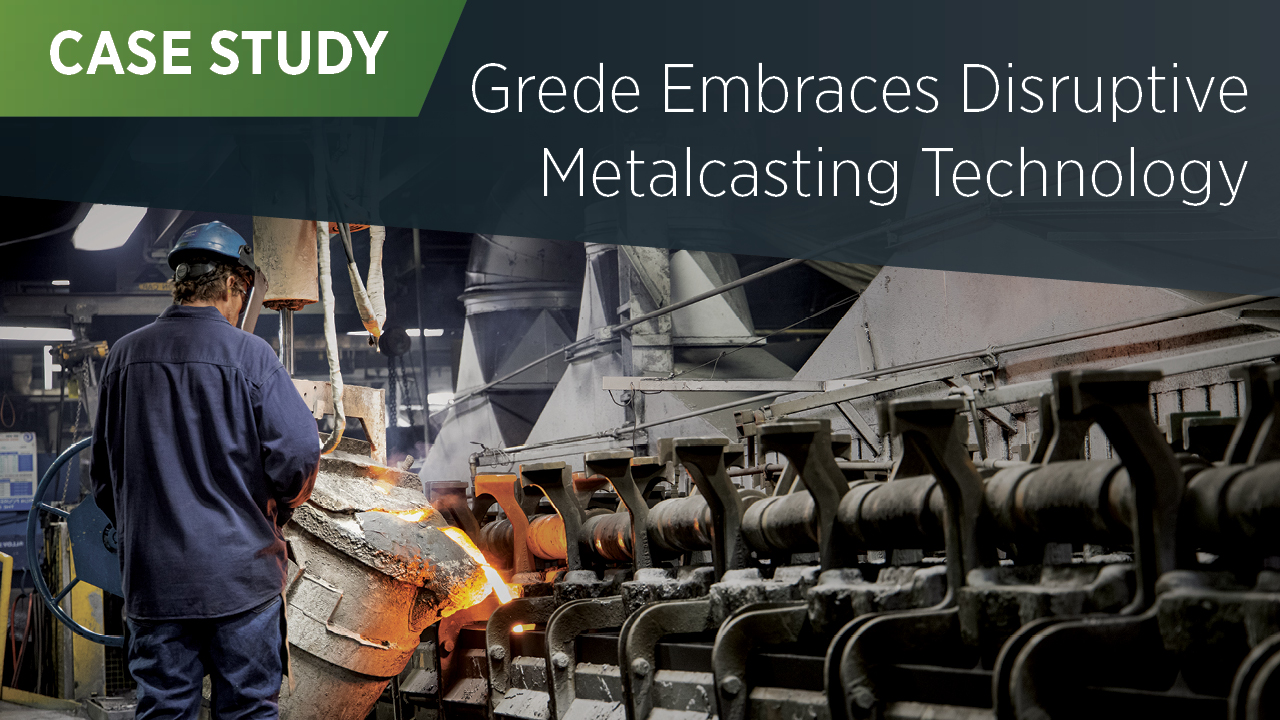
A Century of Experience Embracing Disruptive Metalcasting Technology
Grede, a 100+-year-old iron foundry, leads 3D printing innovations with serial core production
Case Study: Grede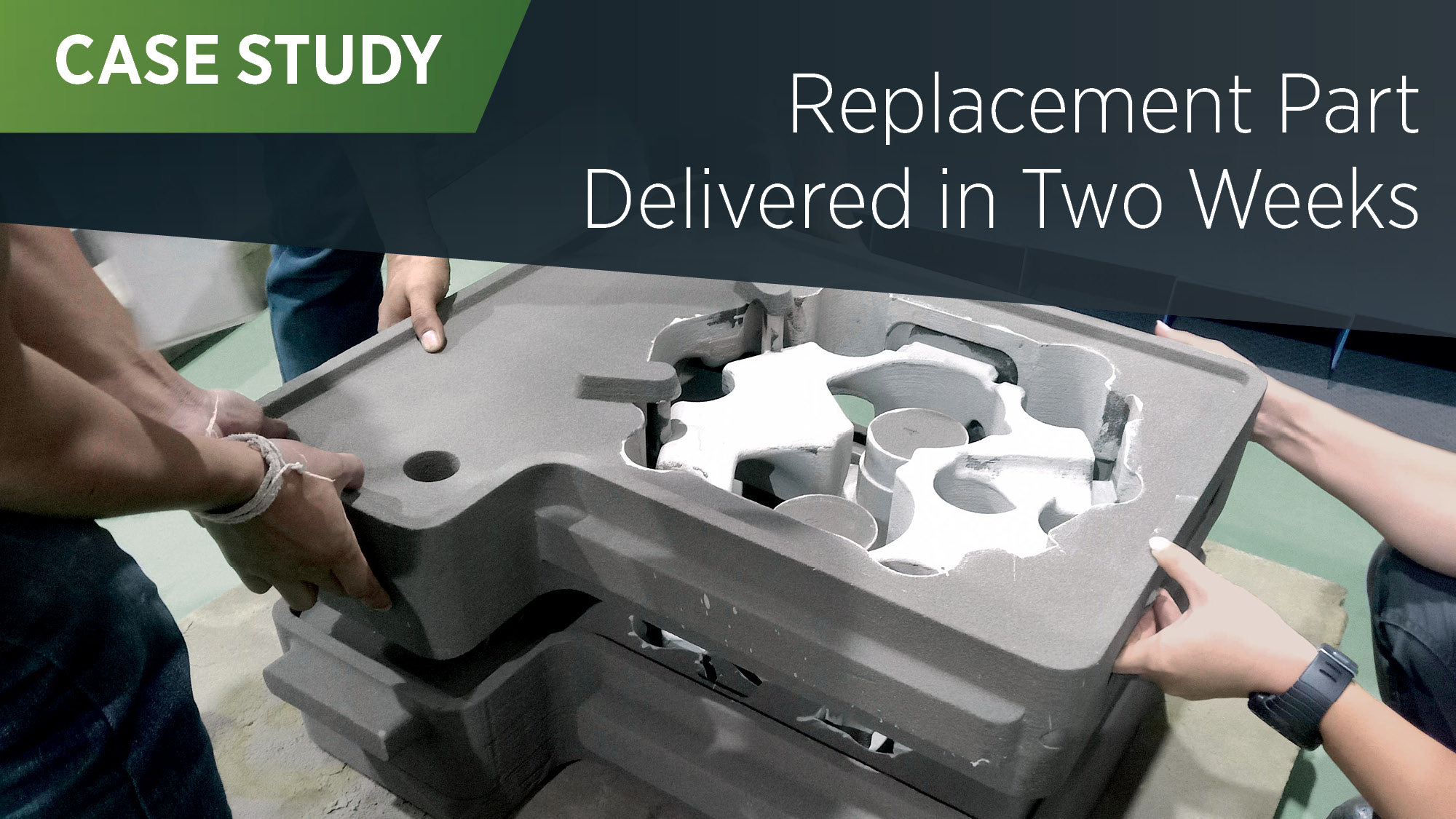
Digital scanning and S-Max 3D printer create casting of obsolete cylinder head
Speed 3D Mold uses binder jetting to cast a replacement gray iron cargo ship engine component without the cost and lead time of traditional tooling
Case Study: Speed 3D Mold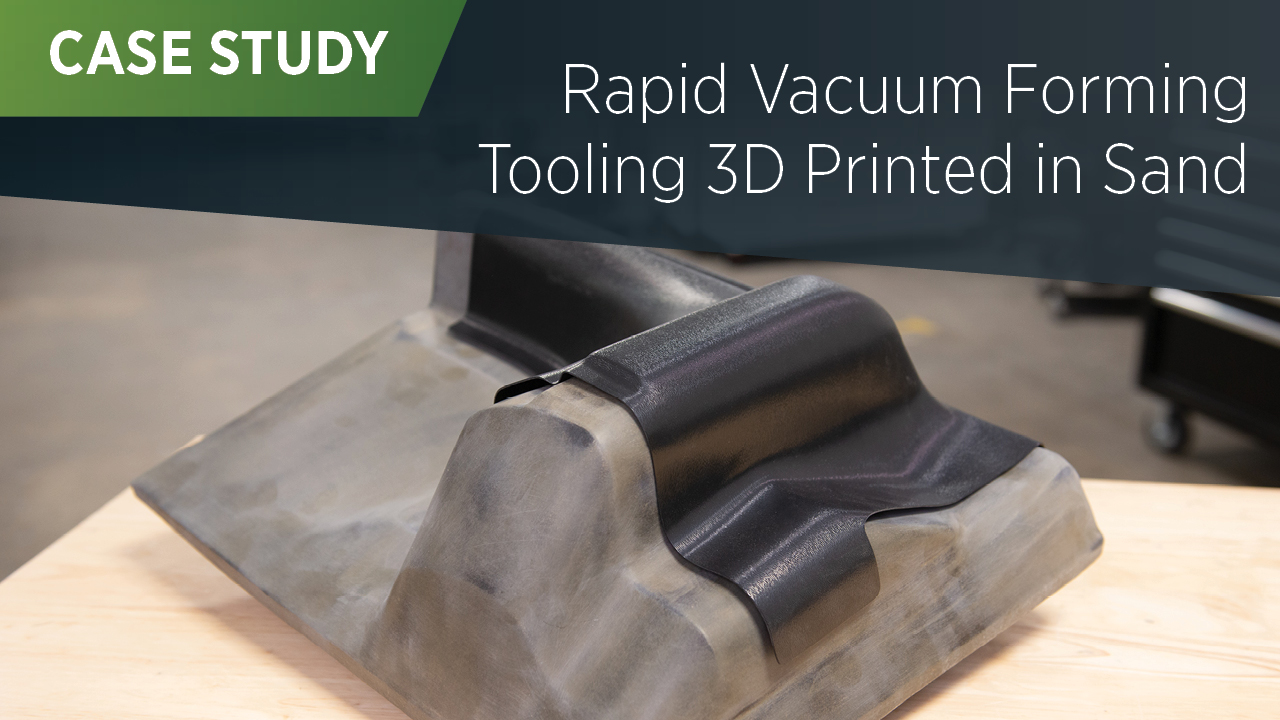
X1 ThermoForm Sand Tooling Proves Durability in Production
Original Appearance Manufacturing get products to market faster with cost-effective, precise, and durable rapid 3D printed sand tooling
Case Study: OAM X1 ThermoForm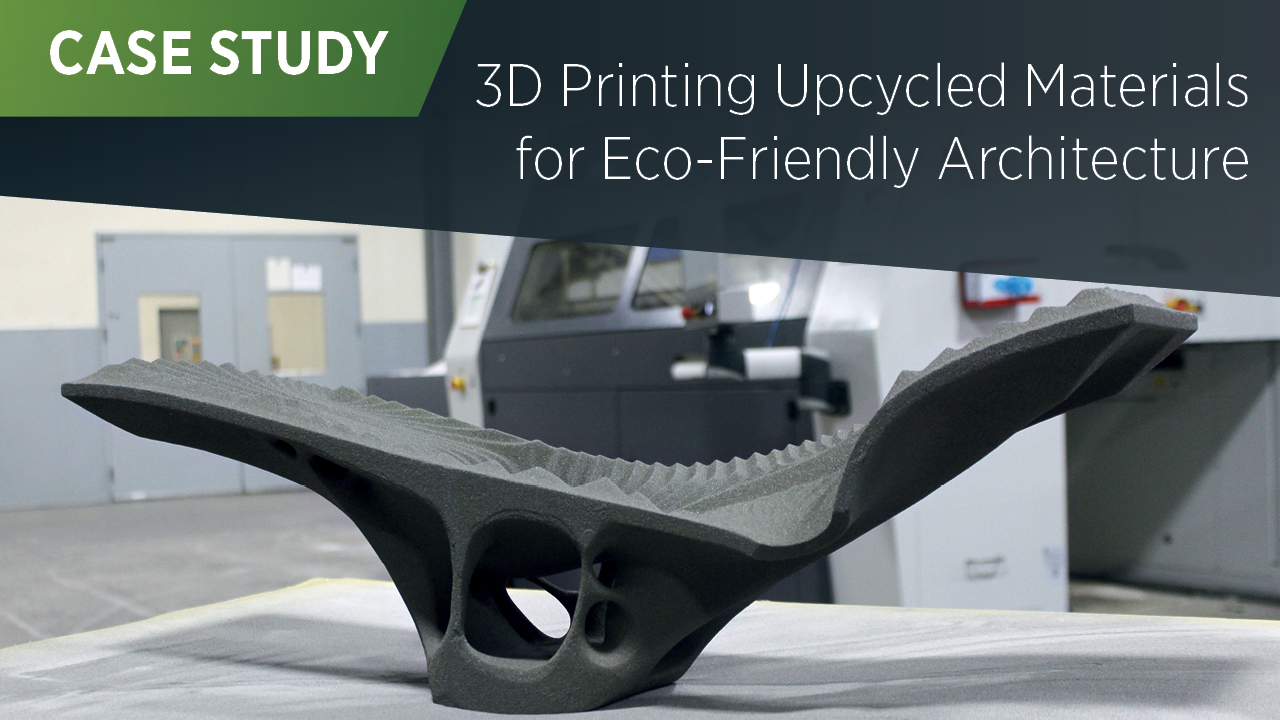
Reinventing Eco-Friendly Architecture and Upcycled Materials with ExOne Binder Jetting
Carnegie Mellon University School of Architecture is shaping the future of building design with 3D printing of concrete and other recycled materials
Case Study: CMU School of Architecture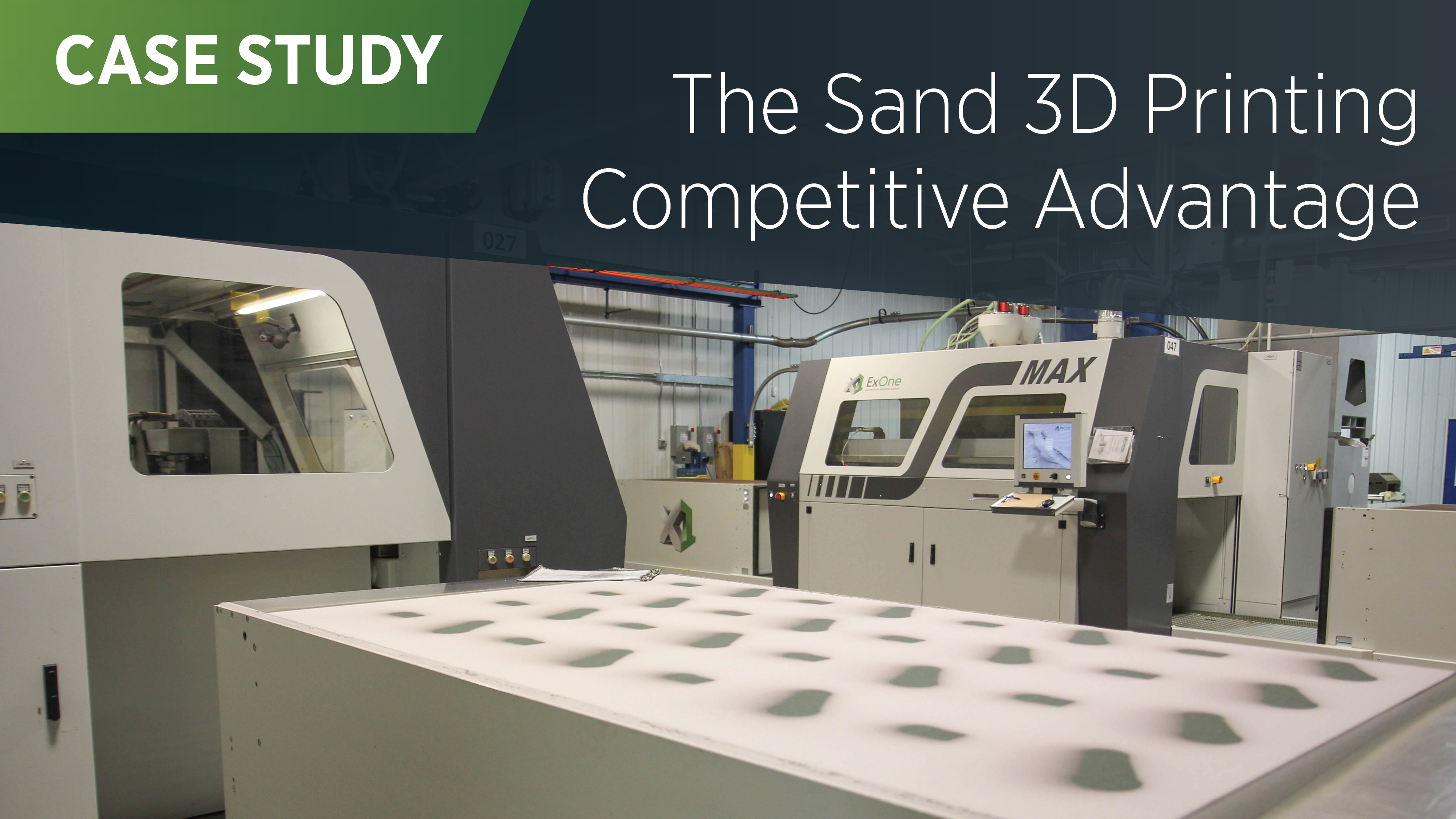
3D Printing Quality Molds Cores Provides Competitive Advantage
Hoosier Pattern embraced additive manufacturing as the first pattern shop in North America to own and operate a sand 3D printer in-house. Today they have four ExOne binder jetting systems.
Case Study: Hoosier Pattern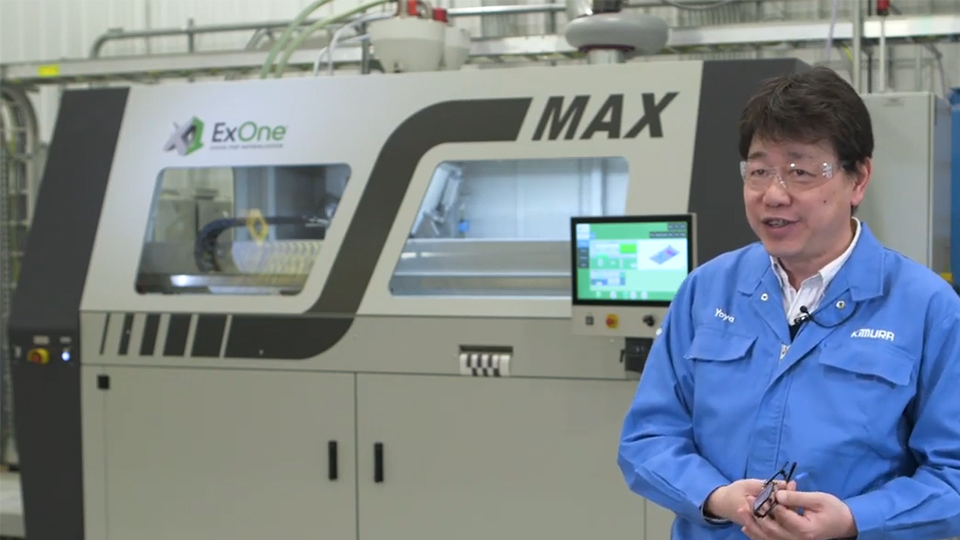
Global Foundry Group Innovates with Sand 3D Printing to Grow Business
With nine decades of experience in sandcasting innovation, Kimura Foundry America places sand binder jetting at the core of its business to deliver top-quality rapid prototypes.
Case Study: Kimura Foundry America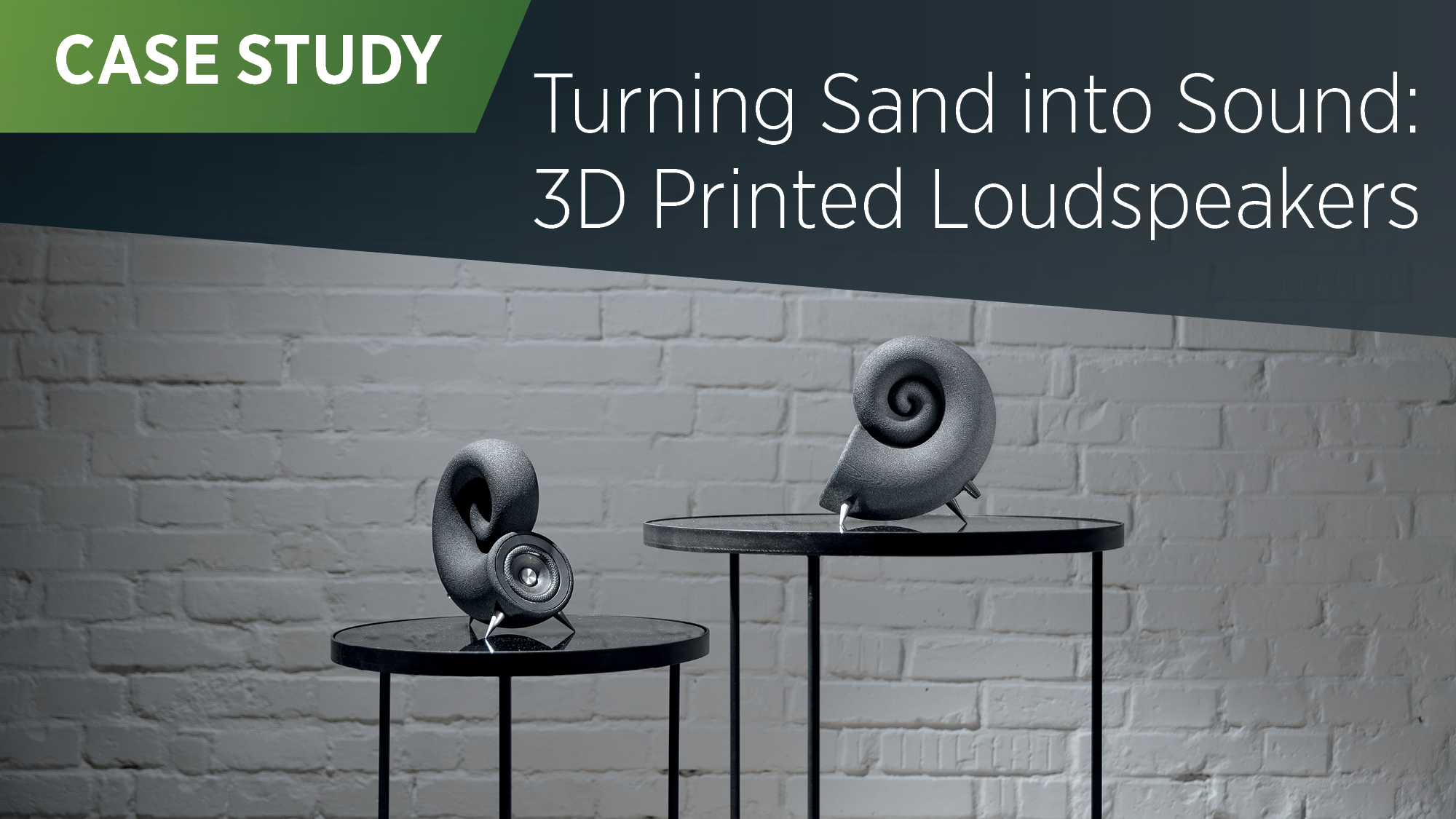
Turning Sand into Sound: 3D Printed Speakers
How a small startup in Czechia is challenging the giants of the audio industry with the help of 3D printing
Case Study: Deeptime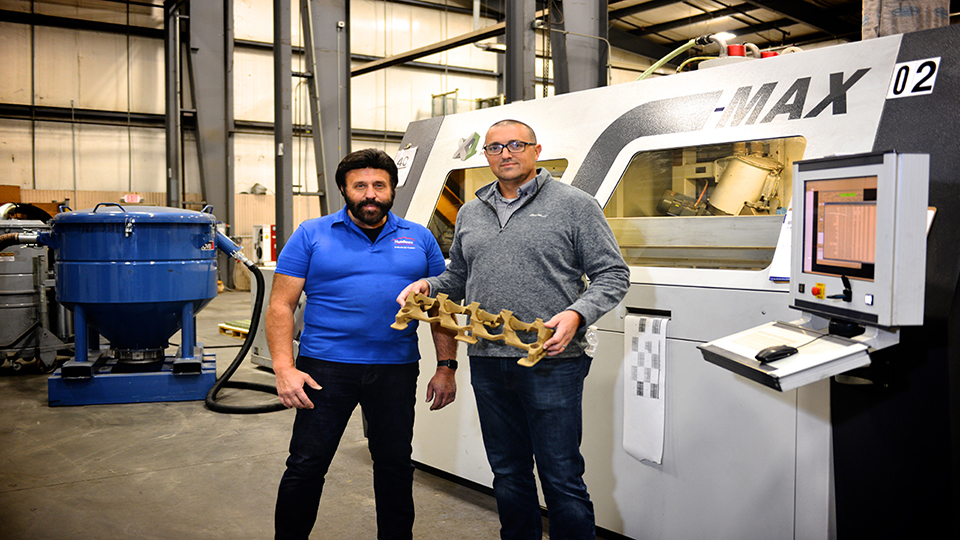
Humtown Products and ExOne
How 3D printing transformed a family-owned manufacturer.
Case Study: Humtown Products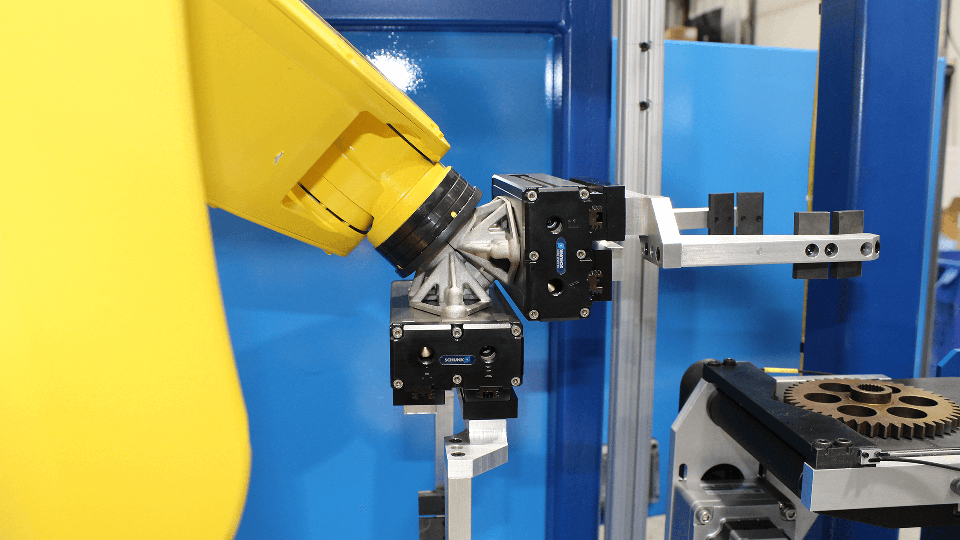
粘结剂喷射案例研究:耐用、轻便且价格实惠的汽车机械手模具
FreeFORM科技公司利用ExOne粘结剂喷射3D打印技术,开发了一项以17-4PH型不锈钢为原料的适用于大批量汽车检测过程的复杂机械手模具解决方案。
CASE STUDY: FreeFORM Technologies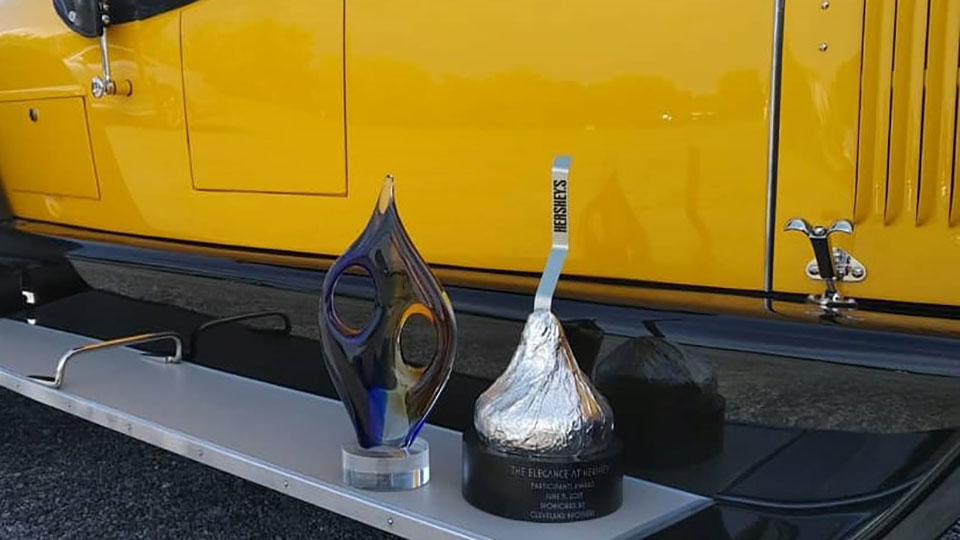
HV3DWorks有限责任公司与ExOne的合作
一位客户正在为2018年加州蒙特雷卵石滩优雅大赛(Pebble Beach Concours d’Elegance)修复一辆1921年生产的Kissel Gold Bug Speedster跑车,他需要重新制作一整套的四个发动机罩闩。
Select Filters Cancel
Applications
Select All
Industries
Select All
News & Events
Select All
Resources
Select All
Systems
Select All
Technology
Select All