- Home
- Binder Jetting Ressources
- Fallstudien
Neue Perspektiven durch 3-D-Druck
Neue Perspektiven durch 3-D-Druck
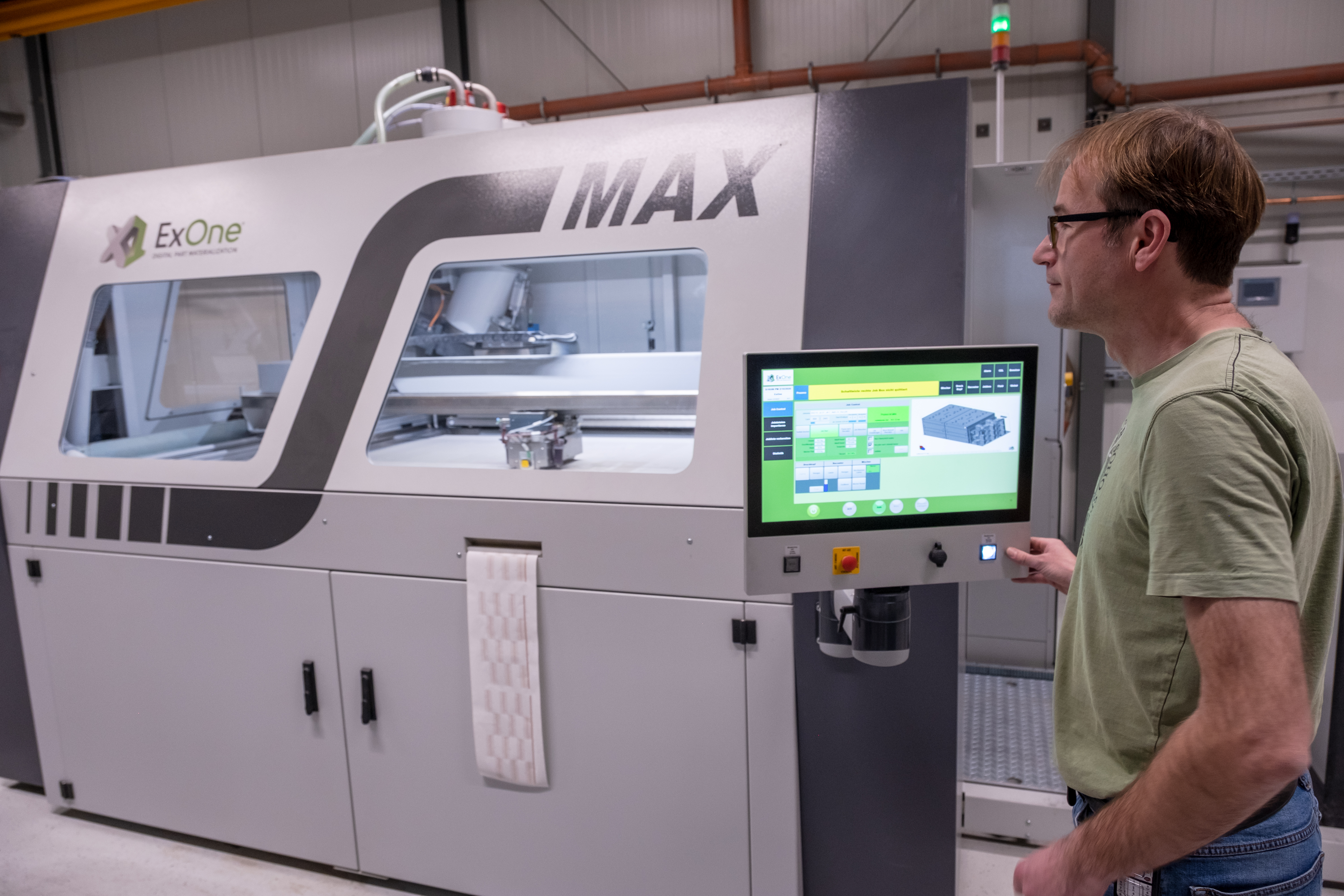
Neue Perspektiven durch 3-D-Druck
Die Prototypengießerei Grunewald im münsterländischen Bocholt hat Ende 2018 in einen 3-D-Sanddrucker von ExOne investiert. Nach über einem Jahr ist die Bilanz mehr als positiv.
Michael Klein-Hitpass steht am Display eines ca. 2 mal 3 Meter großen ExOne-3-D-Sanddruckers vom Typ S-Max Plus. Gerade generiert er einen Baujob für vier Sandformen und eine Reihe von Kernen. Auf dem Bildschirm sieht es ein bisschen so aus, als wenn er eine Runde des Computerspielklassikers Tetris spielt: Die einzelnen Formen und Kerne werden übereinander und nebeneinander eingepasst. Zum Original-Spielambiente fehlt eigentlich nur noch, dass vervollständigte Linien aufleuchten und dann verschwinden, begleitet von elektronischer Spielmusik. Ist die Box voll, startet der Druck und der Druckkopf fährt von einer Seite zur nächsten, bis erste Konturen der gedruckten Teile zu erkennen sind, inklusive Öffnungen, in die später Speiser eingebracht werden. Hier entstehen gerade Formen für Strukturteile sowie Kerne für einen Integralträger, die für ein Versuchsfahrzeug eines englischen Fahrzeugherstellers bestimmt sind.
Gießereileiter Harald Dieckhues und Geschäftsführer Ulrich Grunewald (v.l.n.r.) Das Wachstum durch den 3-D-Sanddruck hat beide positiv überrascht.
Auslastung deutlich besser als erwartet
Der geräumige etwa 60 Quadratmeter große, extrem saubere Raum, in dem das alles stattfindet, enthält neben dem Drucker noch eine Art Auspacktisch neben dem Drucker und eine optische Vermessungseinrichtung. Hinter den großen Sichtfenstern des Druckerraums ist der Ofen zum Härten der Formen und Kerne zu erkennen. Zwischen Schläuchen und Verrohrungen ist an der Decke auch eine gelb lackierte, verfahrbare Kranvorrichtung für den Transport der großen Formen angebracht. Kostenpunkt von Drucker, Peripherie und übrigen Anlagen: 1,3 Millionen Euro.
Klein-Hitpass ist drahtig und groß. Mit seiner Brille nimmt man ihm die Leidenschaft für IT-basierte Gießereianwendungen leicht ab. Sein Berufsweg ging jedoch zunächst in Richtung klassischem Gießer: Modellbauerlehre bei Grunewald, Studium der Gießereitechnik in Duisburg. Über die Diplomarbeit fand er wieder zurück zu seinem Ausbildungsbetrieb in Bocholt. „Ich hätte nie gedacht, dass die Auslastung des 3-D-Druckers so gut ist“, sagt er. Und seine Chefs, Ulrich Grunewald, Geschäftsführer der gleichnamigen Unternehmensgruppe mit Standorten in Bocholt und Irxleben, sowie Gießereileiter Harald Dieckhues stimmen ihm da auf ganzer Linie zu.
Prototypenbauteile für E-Fahrzeuge
Nach der Installation der Anlage Ende 2018 waren zunächst halb gefüllte Jobboxen die Regel. Seit dem Frühjahr vergangenen Jahres arbeitet die Maschine nahezu rund um die Uhr. Während die unsichere Lage in der Automobilbranche das Geschäft von Zulieferern konventioneller Fahrzeuge zurzeit bremst, profitiert Grunewald von den Möglichkeiten, die 3-D-gedruckte Formen und Kerne bei Designfreiheit und Leichtbau bieten. Und diese Eigenschaften sind gerade besonders bei den Entwicklern von E-Fahrzeugen gefragt, deren Anteil am Straßenverkehr in den nächsten Jahren ja deutlich steigen soll.
Strukturteile, Antriebstechnik, Fahrwerks- und Motorenteile sowie Batteriewannen fertigen die Bocholter aktuell für die Versuchsfahrzeuge der Automobilisten - immer häufiger mit 3-D-gedruckten Sandteilen, abgegossen mit Aluminium. Grunewald fertigt Bauteile für Fahrzeuge, die noch in Erprobung sind und in seriennahen Versuchen für eine Markteinführung qualifiziert werden, etwa durch Testfahrten im rauen schwedischen Winter.
3-D-Sanddruck treibt die Gussproduktion
Über ein Jahr nach der Installation ist die Anspannung wegen der Höhe des Risikoinvestments endgültig der Freude über die gute Entwicklung gewichen. Wie gut es läuft, zeigt die Umsatzentwicklung der 2013 eröffneten Gießerei am Busskolk in Bocholt. Lag ihr Anteil am Gesamtumsatz des Unternehmens vor Anschaffung des Druckers noch bei rund 50 Prozent, beträgt er jetzt 75 Prozent und gleicht damit den Rückgang in anderen Bereichen von Grunewald aus – z. B. im Werkzeugbau, der überwiegend von konventioneller Fahrzeugfertigung abhängig ist.
Die gestalterische Freiheit ist ein Argument, das für den 3-D-Druck spricht. Es gibt Kerne und Formen, die wegen ihrer Komplexität nur per additiver Fertigung realisiert werden können. Wenn die dann noch gießbar sind, ist die aktuelle technologische Grenze der Gießereitechnik erreicht. Hinzu kommt die Geschwindigkeit der Drucker. „Je nach Bauteil, Komplexität und Auslastung sind wir mindestens 4-6 Wochen schneller als bei konventioneller Gussteilherstellung“, nennt Ulrich Grunewald den Hauptgrund für die Anschaffung der High-Tech-Maschine. Eine Jobbox mit 1260 Litern Formsand (2,14 Tonnen) ist in 24 Stunden fertig.
Mehr Möglichkeiten für Kunden und Konstrukteure
Zeit war auch ein Argument des Kunden, für den bald die größte „Serie“ seit jeher bei Grunewald gefertigt wird: 1500 Fahrwerksteile, die komplett mit gedruckten Sandteilen realisiert werden. Der Kunde hatte die Wahl, ob er für die Fertigung in eine Druckgießform investieren oder sich die Komponenten mit zum Teil gedruckten Formen im Sandgießverfahren herstellen lassen wollte. Letzteres war günstiger und machte das Rennen. Wer es nicht so eilig hat und auch nicht allzu komplexe Teile benötigt, kann aber weiterhin Gussteile in Auftrag geben, die mittels Modelleinrichtung oder sandgefrästen Formen und Kernen gefertigt werden.
Auch jede Kombination aus gedruckten Sandteilen und per Modelleinrichtung hergestellten Formen und Kernen ist möglich. Neue Fertigungsoptionen, die dankbar von den Kunden angenommen werden. Mit dem Drucker verbinden sich bei Grunewald somit eine ganze Reihe weiterer Vorteile, an die vor der Anschaffung voraussichtlich noch kein Gedanke verschwendet wurde. „Wir werden mit dem Drucker auch direkt als Technologiefirma wahrgenommen“, haben Grunewald und Dieckhues darüber hinaus beobachtet. Der Technologiesprung durch 3-D-Drucker feilt also mit am Image moderner Gießereien.
Zudem ändert sich die Denke: „Unsere Konstrukteure denken inzwischen ganz anders, weil es die Möglichkeit gibt, Formen und Kerne auch zu drucken, statt sie nur auf unserer halbautomatischen Formanlage zu fertigen“, weiß Grunewald. Da wird schon einmal ein Kern mitgedruckt, wenn noch Platz in der Jobbox ist. Freiheiten, die es nicht gibt, wenn gedruckte Sandteile teuer zugekauft werden müssen.
Filigraner Feinprozess mit Tücken
Im Druckerraum ist die Diskussion inzwischen bei den Kosten des 3-D-Druckens angelangt. „Im Vergleich zu einem geschossenen Kern ist ein gedruckter weiterhin sehr teuer“, informiert Dieckhues. Die landläufige Meinung, dass dafür die hohen Stromkosten verantwortlich seien, trifft dem zum Gießereimeister an der Wilhelm-Maybach-Schule in Stuttgart ausgebildeten heutigen Gießereileiter zufolge nicht zu. Energie steht nach Wartung und Chemie – also Binder und Sand – erst an dritter Stelle.
„Es ist ein filigraner Feinprozess, kein Vergleich mit den robusten Gießereianlagen, die wir sonst einsetzen“, beschreibt Grunewald. Druckköpfe können verschleißen und ihr Ersatz kann fünfstellige Beträge verschlingen, was die Wartung entsprechend teuer und aufwendig macht. Um von den Vorteilen der Anlage zu profitieren, ist darüber hinaus gut geschultes Personal erforderlich, denn der Prozess ist komplex und die möglichen Probleme vielfältig.
Tatsächlich experimentiert die Firma Grunewald schon seit über 25 Jahren mit der Technologie, die seit Mitte der 1990er-Jahre als Rapid Prototyping bekannt ist. Das frühere Sandsintern versprach aber noch mehr als es halten konnte: die Teile waren entweder zu weich oder zu hart und konnten daher nicht eingesetzt werden. Schon damals beschäftigte sich Klein-Hitpass mit der Technik. Seither steht ihm auch eine Kollegin zur Seite, die ursprünglich Modellbau bei Grunewald gelernt und ebenfalls langjährige Erfahrung mit dem 3-D-Drucken hat. Beim Einsatz der heutigen Maschinen zahlt sich das Know-how der beiden Experten jetzt aus.
Klein-Hitpass demonstriert das mühelose Entsanden von Kernen nach dem Druck. Möglich macht das der eigesetzte Phenol-Kaltharzbinder von ASK Chemicals.
Binder sorgt für geringe Nacharbeit
Beim Blick durch das Sichtfenster des Druckers wird etwa jede halbe Minute eine weitere Schicht aufgetragen und dabei von ASK Chemicals gelieferter Phenol-Kaltharz-Binder mit dem Sand verklebt. Vorteil dieses Binders im Vergleich zum gängigen Furanharz ist die geringere Nacharbeit – der Restsand kann einfach abgeschüttelt werden, während er beim Furanharz an den Sandteilen kleben bleiben kann. Klein-Hitpass demonstriert das an einem der Kerne, die auf einer Palette an der Wand des Druckerraums stehen. Auf den ersten Blick ist die Reinigung des bereits ausgehärteten Sandteils im wahrsten Sinne des Wortes ein Kinderspiel. Per Sandstaubsauger werden die Teile nach dem Druck gereinigt – dann folgen die Prozessschritte Schlichten und Abguss.
Ob die Zukunft bei Grunewald einmal so aussieht wie im japanischen Unternehmen Kimura, wo die Gießerei rund um die Uhr mit Kernen und Formen aus etwa zehn 3-D-Druckern bestückt wird und keine einzige Modelleinrichtung in Betrieb ist, wird die Zukunft zeigen. „Wir brauchen momentan beides, Modelleinrichtung und Drucker“, räumt Grunewald ein. Statt dem Anfangsproblem, dass die Maschine zu produktiv ist, um sie auszulasten, ist die Kapazität nun fast zu klein und die 24-Stunden-Produktion zu kurz. „Wer weiß, was in zwei Jahren ist“, antwortet Grunewald auf die Frage, ob schon die Investition in einen weiteren Drucker angedacht ist. Jetzt, wo der Prozess verstanden ist, will die Gießerei aber über kurz oder lang zwei weitere Maschinenbediener qualifizieren, um Klein-Hitpass und seine Kollegin zu entlasten.
Ist der 3-D-Sanddrucker bald unentbehrlich?
Wie groß das Potenzial des 3-D-Drucks für die Gießereibranche ist, zeigte sich bei der Sitzung des Arbeitskreises Additive Fertigung im Haus der Gießerei-Industrie in Düsseldorf Ende Januar: Zugeschaltet war ein Vertreter von BMW, der berichtete, dass gedruckte Kerne bereits in der Serienfertigung in Landshut zum Einsatz kommen. „Um die Temperaturen im Motor zu erhöhen, sind gegossene Bauteile erforderlich, deren komplexe Geometrien nur mit gedruckten Kernen möglich sind“, nennt Grunewald die Hintergründe des Fahrzeugbauers, jetzt in großem Stil auf das 3-D-Sanddrucken zu setzen. Ob diese strategische Ausrichtung in der Kernherstellung ein Einzelfall bliebt oder eines Tages zur Regel wird, bleibt abzuwarten.
Bei Grunewald sieht es jedenfalls ein Jahr nach der Einführung des 3-D-Druckers danach aus, als ob die Rechnung aufgeht. Strategie für die Zukunft: Weiter automatisieren, damit die eigenen Fachkräfte Beinfreiheit für ihre Facharbeit haben und zugleich einen auskömmlichen Ertrag zu erwirtschaften, um auch für schlechtere Jahre gefeit zu sein. Eine Planung, die zu einem 200-Mitarbeiter-starken Mittelständler wie Grunewald passt und auf langjährigen und nachhaltigen Fortbestand zielt.
Allmälich zeichnen sich die Konturen der Formen und Kerne im 3-D-Drucker ab,
Gedruckte Formen beim Aushärten. Die gewünschten Bauteile werden immer größer.
Ulrich Grunewald vor der Form eines Aluminiumformwerkzeugs mit integrierter Kühlung für Automobil-Bodenteppiche.
Urheberhinweis, Casting, Plant & Technology 2+3, 2020. Klicken Sie hier um PDF herunterzuladen.