- Home
GF Casting Solutions Leipzig Fallstudie
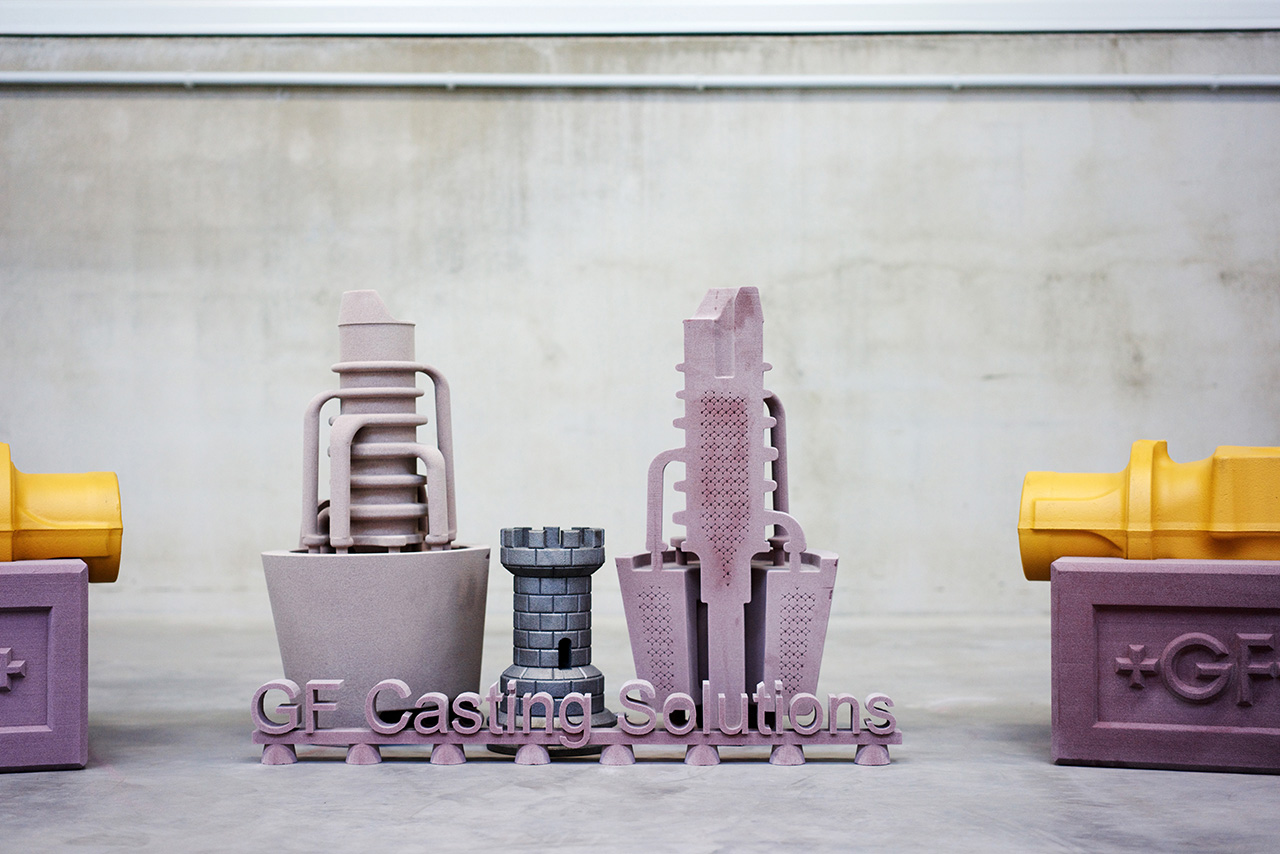
Additive Fertigung komplexer Sandkerne für hydraulische Drehdurchführungen
ExOne Fallstudie
Mit dem 3D-Drucker S-Max von ExOne ist es Georg Fischer Casting Solutions Leipzig GmbH gelungen, 12 geschossene Kerne in einem gedruckten Kern zu konsolidieren.
Neben einer verbesserten Kernqualität fallen dadurch außerdem die zeit- und arbeitsintensiven Schritte zur Kernmontage und Nachbearbeitung weg.
GF Casting Solutions betreibt in Leipzig seit 1995 die Gießerei mit Europas größtem Formkasten für maschinengeformten Eisenguss. In einem vollautomatischen Prozess stellt die Gießerei mithilfe von Modellplatten sogenannte Grünsandformen her, die als Negative für die Gusskontur dienen. Die Kerne werden im Cold-Box-Verfahren geschossen und im Anschluss in die Form eingelegt, um die Innenräume der Gussteile auszubilden. Aufgrund der hohen anfänglichen Investitionskosten, u.a. für Modelle und Kernkästen sowie bei der Prototypenherstellung, war der Produktionsprozess mit einem hohen Kosten- und Zeitaufwand verbunden.
In der Regel kann es mitunter Monate dauern, bis eine Gießerei dem Kunden einen ersten Prototyp vorlegen kann. Bis zu letztendlichen Markteinführung ist daher oft mit erheblichen Verzögerungen zu rechnen. Im Laufe der Zeit wurden die Forderungen nach schnelleren Lieferzeiten und zunehmend komplizierteren Prototypen immer lauter – und mit herkömmlichen Produktionsverfahren war dies kaum zu realisieren.
Finden Sie in der Fallstudie heraus:
- Warum die Gießerei in die 3D-Sanddrucktechnologie von ExOne investiert hat.
- Die neuen Anwendungen der Gießerei mit 3D-Druck über das Rapid Prototyping hinaus.
- Wie die Gießerei 12 geschossene Kerne für hydraulische Drehdurchführungen in einem einzigen gedruckten Kern konsolidiert hat.
- Die Vorteile, die die Gießerei durch die Nutzung der 3D-Sanddrucktechnologie erzielt hat.
- Ausbau der Fertigungskapazitäten der Gießerei.
„Der Kern für die Drehdurchführung zählt zu den komplizierteren Kernen, die wir in unserer Gießerei verwenden. Bei der konventionellen Fertigung waren 12 Kerne erforderlich, um die Hinterschneidungen und dünnen Kanäle zu erreichen. Die Montage dieser Kerne ist zeitaufwändig und fehleranfällig. Mit dem 3D-Drucker können wir den gesamten Kern in einem Stück fertigen.“
Eric Nierenberg
Technologe
GF Casting Solutions Leipzig GmbH