
3D Printed Sacrificial Tooling that Washes Out with Water
Washout tooling solutions streamline the production of aircraft ducting, pressure tanks, struts, mandrels and other hollow objects by 3D printing sacrificial tool cores in sand that washes out with water and is reclaimed for reuse.
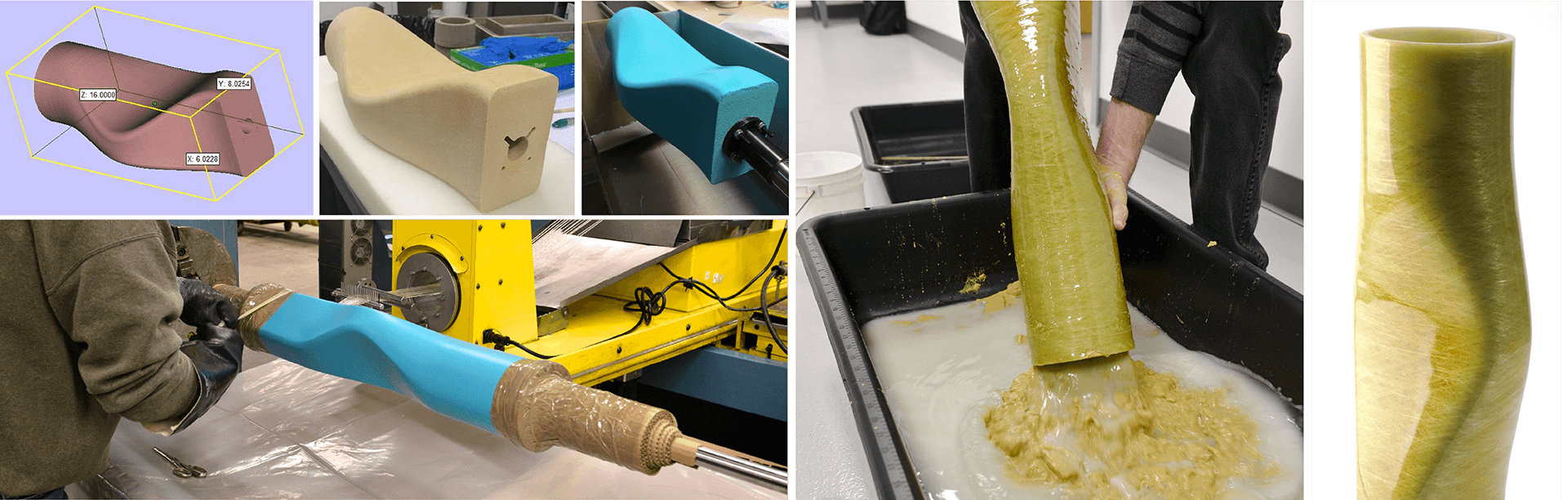
3D Print. Coat. Layup. Rinse & Repeat.
ExOne 3D prints your tool in sand, and coats it in a proprietary material. You lay up carbon- or glass-fiber parts on the tool as normal, autoclaving up to temperatures of 180° Celsius or 356° Fahrenheit. When complete, the sand tool washes away with tap water. Sand can be reclaimed for reuse.
Let ExOne 3D Print Your Washout Tooling
Our high-quality service is fast and affordable.
request a quote for x1 washout toolingLet ExOne 3D Print Your Washout Tooling
Our high-quality service is fast and affordable.
request a quote