Binder Jetting Accessories
We're committed to developing an end-to-end digital workflow that starts with your digital file and uses software, automation and AI to streamline the entire ExOne 3D printing process until your parts are finished.
New solutions that allow you to digitally monitor and analyze your 3D printing work cell, and provide convenient alerts, are just some of the new solutions from ExOne. Our R&D department is hard at work streamlining production for our cutting-edge binder jetting systems. What's on the horizon? Automated desanding stations. AGVs that take your parts from one step to the next. New printhead designs that make replacements of modules quick and easy.
Our Product Family
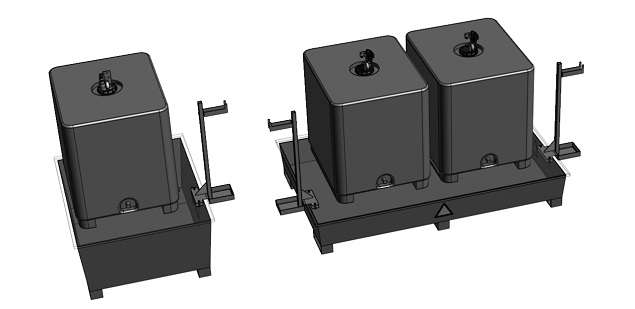
Fluidmatic
Updated for 2024, Fluidmatic v3 is a system for the automatic supply of liquid binder and cleaner to ExOne sand binder jetting systems
accessory detail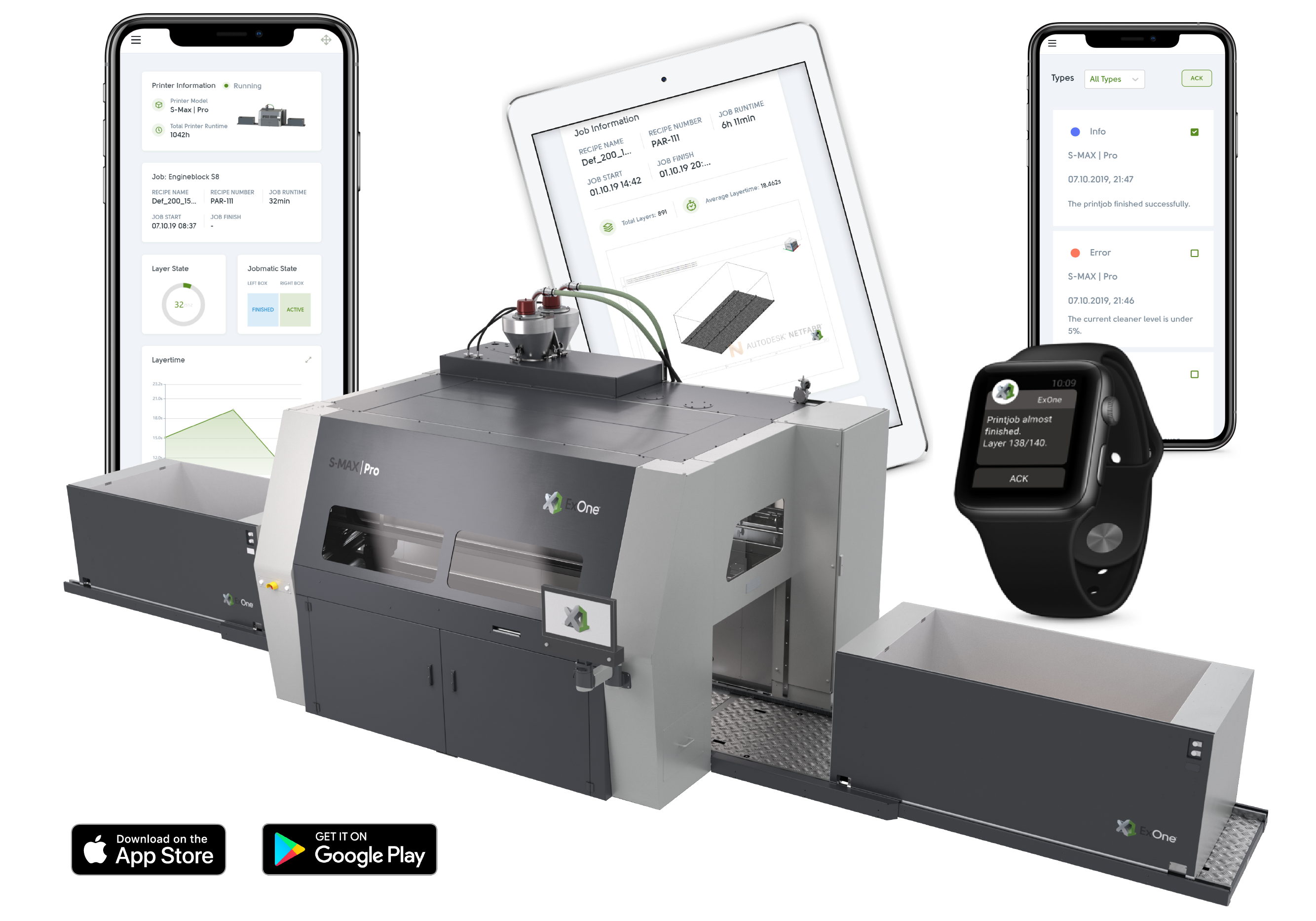
ExOne Scout
ExOne Scout is a secure Industry 4.0 app that provides real-time machine monitoring and analysis of ExOne production 3D printers on a wide range of digital devices, including smart phones and watches.
- Real-time machine monitoring
- Live insights and analysis
- Enhanced quality assurance
- Full reporting capabilities
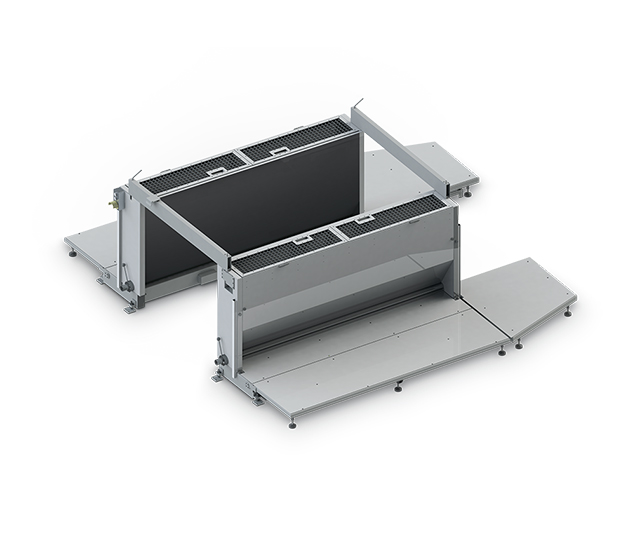
Desanding Station
In the future, the S-Max and S-Max Pro printers will make the 3D printing of cores and molds significantly more agile and therefore smarter. This is all possible thanks to a semi-automatic desanding station for your jobbox: the technological solution that significantly accelerates the jobbox desanding process. The desanding station can be installed and retrofitted efficiently on all S-Max and S-Max Pro models.
- Quickly desand the jobbox thanks to partial automation
- Reduce time and costs spent depowdering parts
- Efficiently use your jobbox by keeping it ready for use
- Lighten workload of system operator
- Intuitive operation simplifies material recycling
- Helps keep your production environment clean
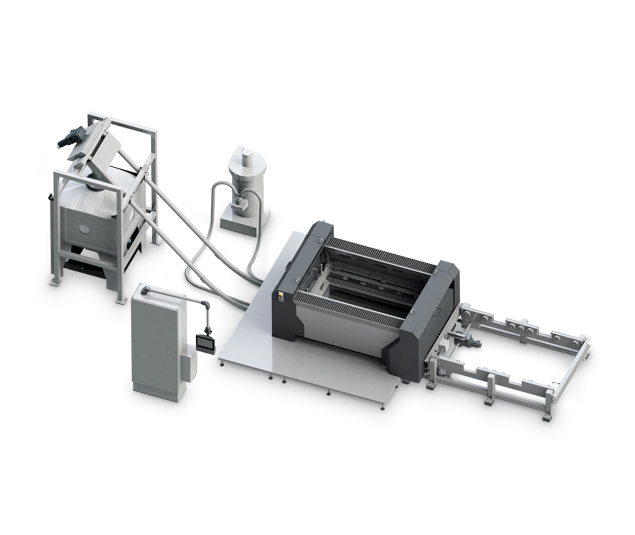
Automated Desanding Station
The pioneering automation technology in the ExOne desanding station can reduce job box material removal time by up to 95%. A state-of-the-art PLC system and integrated sensors save labor costs and increase the speed of desanding cores printed using inorganic binders.
- Fully automated desanding of 3D printed cores
- Increased Overall Equipment Efficiency (OEE)
- Improved ergonomics and work safety
- Future connection to integrate robotics enabling fully automated unpacking and fine desanding