PumpWorks Castings LLC
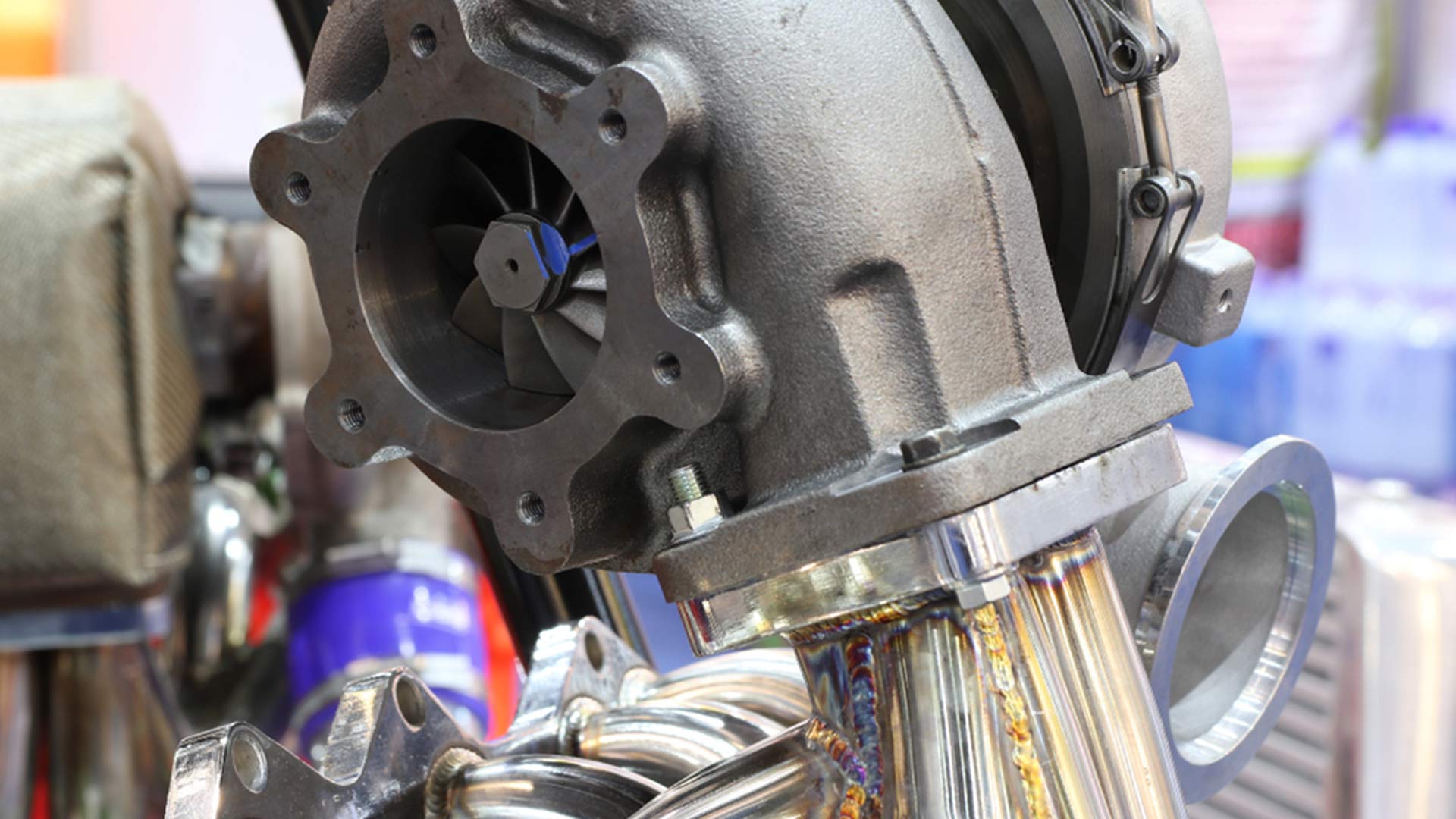
PumpWorks Castings LLC
Reducing lead time from an estimated 17+ weeks down to 8 weeks without tooling
Documentation
Download PumpWorks Castings
Complex Mold Production Reduces Lead Time by 9 Weeks & Saves Thousands