- Home
- Binder Jetting Resources
- Blog
ExOne Expert: Mihaela Nastac
ExOne Expert: Mihaela Nastac
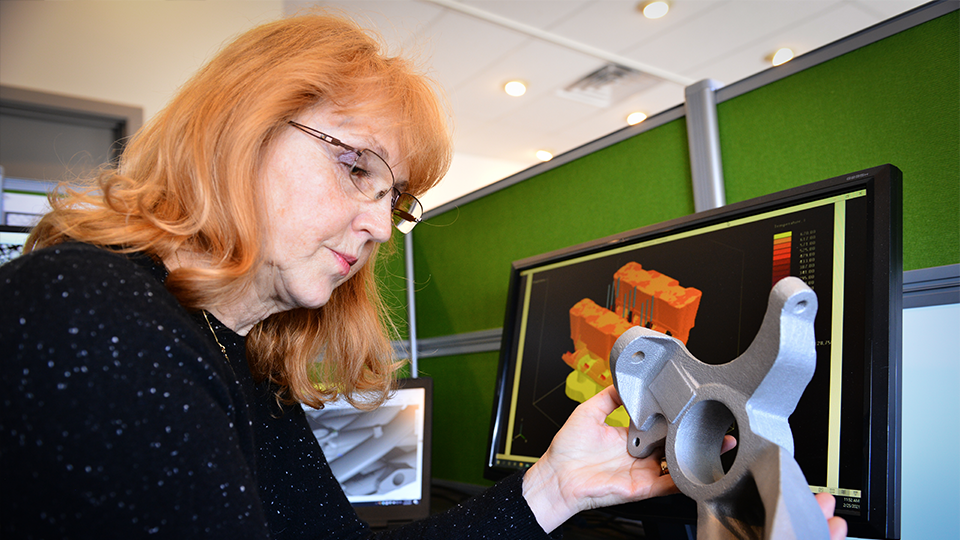
ExOne Expert: Mihaela Nastac
Our Senior Metallurgical Engineer supports some of the world's most challenging 3D printed casting projects, making sure they meet their objectives with done-in-one pours.
In 15 years with ExOne, Mihaela Nastac has established a reputation as the digital casting expert. Not only does she assist customers in optimizing core and mold designs for 3D printing but, at their request, often shows up to the foundry to oversee the pour and ensure success through an end-to-end scientific approach. When asked about her value to customers, Jesse Blacker, Director of New Products & Business Development at ExOne, emphasized how customers benefit from her hands-on approach to ensure the success of their casting:
"Mihaela brings an extraordinary level of metallurgical technical expertise in the sandcasting industry together with a progressive and forward-looking design approach that fully leverages additive manufacturing’s potential. She can predict with an incredible degree of accuracy the likelihood of casting success or not prior to pouring any metal and she can be found on the foundry floor during pours to provide post-casting metallurgical analysis. Her combination of design, modeling and simulation, and hands-on casting expertise brings value to every OneCast project."
We spoke with her about her role supporting customers and how she enjoys working to develop each project step-by-step.
They were developing an all-new gearbox for a completely new helicopter model, so everything was a brand-new casting. On very complex projects such as these, it is common to have at least 10 trial castings and their team was amazed when we got it right the first time. When you have the technology that we have it gives you the freedom to do whatever you want without patterns and at speeds casting customers aren’t used to.
Mihaela Nastac, ExOne Senior Metallurgical Engineer, recalls a project for Sikorsky.
Starting her career as a foundry plant engineer and then a researcher with the National Research Institute of Romania, Mihaela Nastac was drawn to the science of solidification modeling. She obtained her master’s degree in Metallurgy with a specialty in foundry techniques including solidification theory and casting solidification processes. “I enjoy the complexity of putting all the pieces of the puzzle together,” said Nastac. “It’s a technological process where we use a scientific based approach for rigging design with a mix of metallurgy, chemistry, and physics because every alloy is different, and you design based on geometry, the soundness requirement, and the chosen material.”
The key to a successful casting is to envision all the pieces of the puzzle at the start and have a clear idea of what the end vision for success is, Nastac believes. “That’s the goal behind OneCast design services from ExOne that I support. Lots can go wrong with high-value, complex castings and it’s my job to combine the science of the metal and the engineering of the rigging design to support successful first pours and provide good castings to customers in a fraction of the time,” she said.
Despite the rapid progression of design innovation, Nastac points out that only some foundries are able to offer engineering around complex castings. Bridging that gap is where she comes in, combining her knowledge of the possibilities binder jetting offers with virtual modeling to ensure manufacturers’ castings are successful at their foundry of choice. Emphasizing the freedom of design 3D printing has opened up, she explained how organic geometries can affect elements like the sprue, runner, gates, and risers. “Additive manufacturing allows us to use hyperbolic sprue shapes to reduce the velocity of the liquid metal entering the mold cavity. Or we can easily create bottom gating design, or multiple level runners to eliminate defects related to turbulence from gravity pour without the limitation of traditional patterns. We determine where the soundness of the casting will benefit the most and adjust the design appropriately.”
A “virtual casting” is essential to done-in-one-pour success, Nastac emphasized. “Through my modeling I can tell customers with 95% certainty whether this will be a good casting, pointing out areas where they are likely to need some repairs,” she explained describing the free-flowing solidification software she uses to identify macro and micro shrinkage. In an iterative process she analyzes the data to optimize the orientation and hot spots while developing designs to integrate organic rigging designs and validate solidification parameters.
This kicks off the chain reaction in benefits of using binder jetting technology to 3D print molds and cores for casting. “We work on virtual castings to eliminate prototype iterations that need to be poured. Modeling guides the design and modifications can be made quickly to virtual castings to optimize the geometry before it reaches the foundry,” she said, noting that the speed of these iterations is the main benefit to customers. “In the traditional process, core and mold tooling would be built for the design. This could take up to six months and is also very expensive. But that is the traditional way, that you could only know if a casting would be successful when you poured it and any changes to the design was practically starting all over with a new casting. Today, binder jetting allows us to print straight from CAD models, so we iterate the design as we work with the modeling and 3D print cores and molds in just a few days direct from the CAD model.”
Not only are these changes made quickly, but the fact that they can be made at all is still novel to the industry, she continued. “We used to be very geometry limited without the freedom of creating complex rigging design. Binder jet 3D printing eliminates the need for drafts to extract traditional molds, we simply have to brush sand off our pattern. We don’t have to design around the cutting lines of traditional patterns, allowing us to place elements, like those bottom gates or risers for instance, where it’s best for the casting, not where it’s most convenient for the pattern.”
To summarize Nastac recalled a project for Sikorsky. “They were developing an all-new gearbox for a completely new helicopter model, so everything was a brand-new casting. On very complex projects such as these, it is common to have at least 10 trial castings and their team was amazed when we got it right the first time. When you have the technology that we have it gives you the freedom to do whatever you want without patterns and at speeds casting customers aren’t used to.”
ExOne Makes Done-in-One Pours Possible
Mihaela and our team of experts are available to help customers innovate and succeed with binder jet technology to revolutionize sandcasting.
Get started with your own onecast project