Digital Foundries Deliver Critical Replacement Castings, Fast
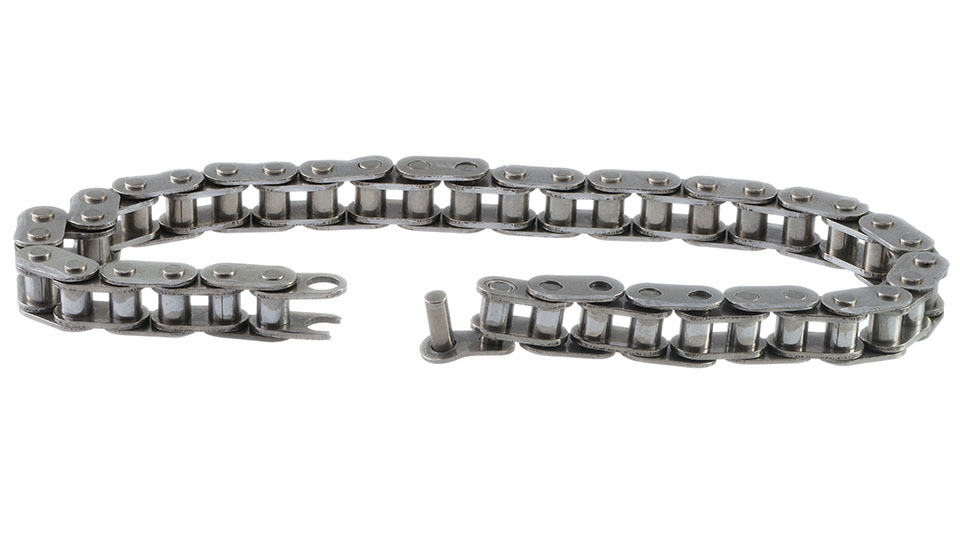
Digital Foundries Deliver Critical Replacement Castings, Fast
Sand 3D printing strategies support de-risked supply chains by producing foundry molds and cores direct from digital models that drastically decrease lead times, tooling investment and casting defects
Need a fast replacement casting?
Connect with us to find an ExOne sand 3D printer in your area to support your needs
Get started today